Plastics sucking molding machine and plastics sucking molding method
A plastic forming machine, an organic technology, applied in the field of plastic forming machines and plastic forming, can solve the problems of temperature inconsistency, large energy consumption, uneven heat dissipation, etc., to ensure constant temperature and avoid low or excessive temperature high effect
- Summary
- Abstract
- Description
- Claims
- Application Information
AI Technical Summary
Problems solved by technology
Method used
Image
Examples
Embodiment Construction
[0022] The specific implementation manners of the present invention will be described in detail below in conjunction with the accompanying drawings. Apparently, the described embodiments are only part of the embodiments of the present invention, and other embodiments obtained by those skilled in the art without creative efforts all belong to the protection scope of the present invention.
[0023] A method for blister forming, comprising the steps of:
[0024] S1. Start the heating system to heat the upper and lower molds, and adjust the temperature of the upper and lower molds through the temperature control system. According to the specifications of the workpiece, the temperature is controlled between 85 and 200 degrees;
[0025] S2. Place the workpiece in the lower mold and preheat it;
[0026] S3. Turn on the vacuum suction device, and vacuum-form the preheated workpiece downward.
[0027] Such as figure 1 The blister forming machine provided by the present invention in...
PUM
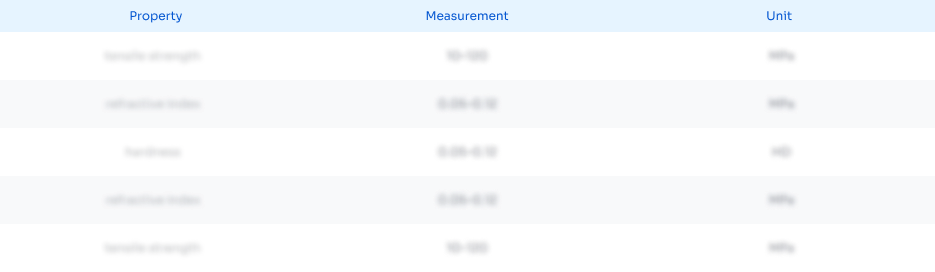
Abstract
Description
Claims
Application Information

- Generate Ideas
- Intellectual Property
- Life Sciences
- Materials
- Tech Scout
- Unparalleled Data Quality
- Higher Quality Content
- 60% Fewer Hallucinations
Browse by: Latest US Patents, China's latest patents, Technical Efficacy Thesaurus, Application Domain, Technology Topic, Popular Technical Reports.
© 2025 PatSnap. All rights reserved.Legal|Privacy policy|Modern Slavery Act Transparency Statement|Sitemap|About US| Contact US: help@patsnap.com