Machine tool electrical spindle reliability testing stand centering adjusting device
A technology of centering adjustment and electric spindle, which is applied in the testing of machine gears/transmission mechanisms, etc., can solve problems such as difficulty in increasing speed, inability to detect misalignment, and exacerbated bearing life, so as to avoid reduction in stiffness and natural frequency and improve versatility And flexibility, the effect of increasing the test speed
- Summary
- Abstract
- Description
- Claims
- Application Information
AI Technical Summary
Problems solved by technology
Method used
Image
Examples
Embodiment Construction
[0033] The present invention will be described in detail below in conjunction with the drawings:
[0034] Refer to figure 1 , The centering adjustment device of the machine tool electric spindle reliability test bench, including a ground iron 2, a control cabinet 1 and a dynamometer 7 that loads the simulated cutting torque for the tested electric spindle 10, the tested electric spindle 10 is the machine tool electric spindle The high-speed electric spindle that needs to be tested in the reliability test. The input shaft of the dynamometer 7 is connected with the measured electric spindle 10 through the elastic diaphragm coupling 8 and the coaxial key. It also includes the rotary table 3, the XZ table 4, and the lifting Table 6 and tilting table 5;
[0035] Refer to figure 1 , figure 2 ,with Figure 5 , The rotary table base 11 at the bottom end of the rotary table 3 has long holes processed on both sides, which are fixed on the right side of the ground iron 2 by T-bolts and nuts,...
PUM
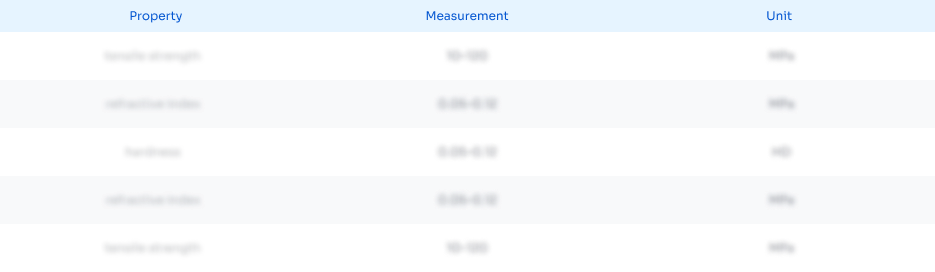
Abstract
Description
Claims
Application Information

- Generate Ideas
- Intellectual Property
- Life Sciences
- Materials
- Tech Scout
- Unparalleled Data Quality
- Higher Quality Content
- 60% Fewer Hallucinations
Browse by: Latest US Patents, China's latest patents, Technical Efficacy Thesaurus, Application Domain, Technology Topic, Popular Technical Reports.
© 2025 PatSnap. All rights reserved.Legal|Privacy policy|Modern Slavery Act Transparency Statement|Sitemap|About US| Contact US: help@patsnap.com