Butenedioic acid resin, preparation method thereof, and preparation of aluminum-casted crystallizer demoulding oil therewith
A technology of butenedioic acid and butenedioic anhydride, which is applied in the field of mold release, can solve problems such as difficult filling, high kinematic viscosity, and long capillary time, and achieve good lubricity, high kinematic viscosity, and less carbon residue Effect
- Summary
- Abstract
- Description
- Claims
- Application Information
AI Technical Summary
Problems solved by technology
Method used
Image
Examples
Embodiment 1
[0032] Step 1, add 116.07kg (1000mol) of fumaric acid and 354.12kg (1900mol) of lauryl alcohol in the polymerization kettle, add 28kg of dilute sulfuric acid (5%), charge into nitrogen to convert the air in the polymerization kettle to react, after the reaction Decompress and discharge water, which is lauryl fumarate.
[0033] Step 2: Add 1.16kg of dibenzoyl peroxide initiator into the polymerization kettle and stir, keep the reaction temperature at 160°C, after 8 hours of polymerization reaction, discharge the polymer in the polymerization kettle, filter and remove it at a temperature above 100°C, etc. Impurities, that is, fumaric acid laurel resin.
[0034] Stir 75kg of the above lauryl resin fumarate and 25kg of trimethylolpropane trioleate at a temperature of about 100°C for 20 minutes to obtain a release oil for aluminum casting crystallizers, which is naturally cooled and packaged.
Embodiment 2
[0036] Step 1, the maleic acid of 116.07kg (1000mol) and the arachidyl alcohol of 597.1kg (2000mol) are added in the polymerizer, add 71.32kg dilute sulfuric acid (5%), fill into nitrogen and change the air in the polymerizer to react, react After decompression to discharge water, it is peanut ester maleate.
[0037] Step 2: Add 0.58kg of lauroyl peroxide initiator to the polymerization kettle and stir, keep the reaction temperature at 180°C, after 4 hours of polymerization, discharge the polymer in the polymerization kettle, filter and remove other impurities at a temperature above 100°C, It is maleic acid peanut resin.
[0038] Stir 25kg of the above-mentioned peanut ester maleate, 70kg of pentaerythritol tetraoleate, and 5kg of tributyl phosphate at a temperature of about 100°C for 20 minutes to obtain a release oil for aluminum casting crystallizers, which is naturally cooled and packaged.
Embodiment 3
[0040] Step 1, the maleic anhydride of 98.02kg (1000mol) and the stearyl alcohol of 527.59kg (1950mol) are added in the polymerizer, add 12.51kg cation exchange resin, charge into nitrogen and change the air in the polymerizer to react, reduce after the reaction Press out the water, which is stearyl maleate.
[0041] Step 2: Add 0.87kg of tert-butyl hydroperoxide to the polymerization kettle and stir, keep the reaction temperature at 170°C, after the polymerization reaction for 6 hours, discharge the polymer in the polymerization kettle, filter and remove impurities such as at a temperature above 100°C, It is stearyl alcohol maleate resin.
[0042] Stir 50kg of stearyl alcohol maleate resin, 46kg of dipentaerythritol oleate, and 4kg of triisooctanyl phosphate at a temperature of about 100°C for 20 minutes to form a mold release oil for aluminum casting crystallizers. Cool naturally Package.
[0043] The physical and chemical indicators of the above-mentioned aluminum casting...
PUM
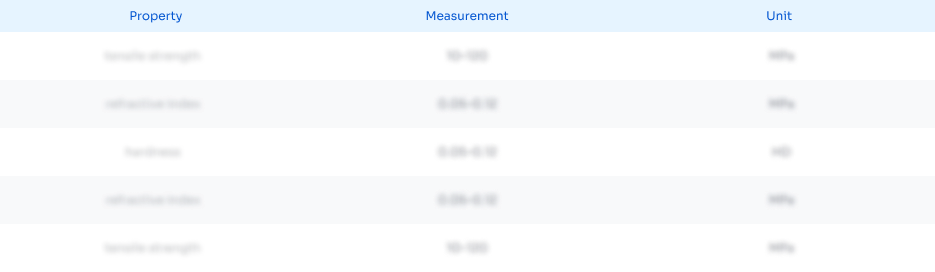
Abstract
Description
Claims
Application Information

- R&D
- Intellectual Property
- Life Sciences
- Materials
- Tech Scout
- Unparalleled Data Quality
- Higher Quality Content
- 60% Fewer Hallucinations
Browse by: Latest US Patents, China's latest patents, Technical Efficacy Thesaurus, Application Domain, Technology Topic, Popular Technical Reports.
© 2025 PatSnap. All rights reserved.Legal|Privacy policy|Modern Slavery Act Transparency Statement|Sitemap|About US| Contact US: help@patsnap.com