Method of processing impeller on five-axis machining center
A five-axis machining center and impeller technology, applied in the field of machining, can solve the problems of impeller flow channel geometric size change, flow channel accuracy error, easy to produce virtual welding, etc., to reduce cutting force and cutting area temperature, improve processing quality and precision, the effect of improving surface roughness
- Summary
- Abstract
- Description
- Claims
- Application Information
AI Technical Summary
Problems solved by technology
Method used
Examples
Embodiment Construction
[0013] The method for machining an impeller on a five-axis machining center includes the following steps:
[0014] The first step is clamping; the mandrel is used for clamping and positioning, the keyway is processed on the blank for auxiliary positioning, and the clamping is made to adapt to the positioning of the mandrel;
[0015] The second step is alignment; use the dial indicator to align the workpiece, find the coordinate system of the workpiece, install the installation rod of the dial indicator on the tool handle, move the worktable so that the center line of the spindle is approximately moved to the center of the workpiece, and make the percentage The contacts of the meter contact the peripheral surface of the workpiece, turn the main shaft by hand, observe the deviation of the pointer of the dial indicator, and move the x-axis and y-axis of the worktable. After repeated repetitions, the pointer of the dial indicator is basically At the same position, it can be co...
PUM
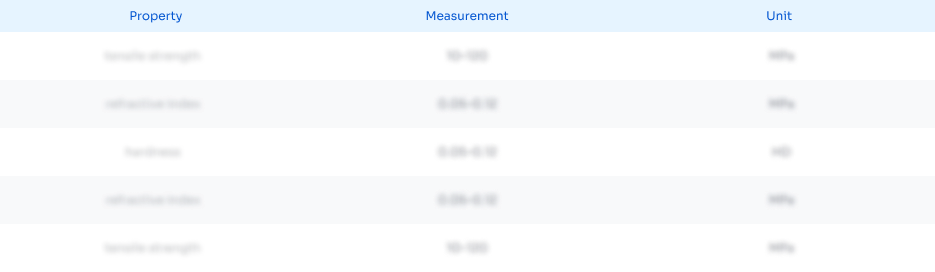
Abstract
Description
Claims
Application Information

- R&D
- Intellectual Property
- Life Sciences
- Materials
- Tech Scout
- Unparalleled Data Quality
- Higher Quality Content
- 60% Fewer Hallucinations
Browse by: Latest US Patents, China's latest patents, Technical Efficacy Thesaurus, Application Domain, Technology Topic, Popular Technical Reports.
© 2025 PatSnap. All rights reserved.Legal|Privacy policy|Modern Slavery Act Transparency Statement|Sitemap|About US| Contact US: help@patsnap.com