Regeneration method for flue gas SCR de-nitration catalyst filtering element
A catalytic filtration and denitration technology, applied in chemical instruments and methods, separation methods, dispersed particle separation, etc., can solve the problems of catalytic filter element filtration efficiency and catalytic activity that cannot meet the requirements, and the filter element cannot be recycled.
- Summary
- Abstract
- Description
- Claims
- Application Information
AI Technical Summary
Problems solved by technology
Method used
Examples
Embodiment 1
[0013] After actually using the catalytic filter element to catalytically filter the flue gas for a certain period of time, the filtration flux and denitrification efficiency are significantly reduced. It is therefore necessary to regenerate the catalytic filter element. In this embodiment, the SCR denitrification catalytic filter element that needs to be regenerated constitutes its catalytic active layer by V 2 o 5 form or with V 2 o 5 As the main component, with WO 3 and MoO 3 At least one of them is a mixture of auxiliary components. In this embodiment, the regeneration method of the flue gas SCR denitrification catalytic filter element comprises the following steps:
[0014](1) Use 0.5MPa compressed air to purge the outer surface of the SCR denitrification catalytic filter element, and then use 1MPa compressed air to carry out multiple backflushing of the catalytic filter element from the inside to the outside;
[0015] (2) After the above-mentioned purging is compl...
Embodiment 2
[0020] The difference between this embodiment and embodiment 1 is that in step (1), 0.4MPa compressed air is used to purge the outer surface of the SCR denitration catalytic filter element, and then 0.8MPa compressed air is used to clean the catalytic filter element from the inside Perform multiple backflushing to the outside; in step (2), soak the catalytic filter element in a dilute sulfuric acid solution with a pH of 5 for 1.5 hours, and then use hot air at 115°C to dry the catalytic filter element for 2 hours; step (3) The concentration of oxalic acid in the active solution is 200mg / L, the concentration of ammonium metavanadate is 80mol / L, the concentration of ammonium metatungstate is 60mol / L, and the catalytic filter element is immersed in this mixed aqueous solution for 3h; In step (4) The impregnated catalytic filter element was baked at a high temperature of 300° C. for 6 hours.
[0021] After the SCR denitrification catalytic filter element is treated by the regenera...
Embodiment 3
[0023] The difference between this embodiment and embodiment 1 is that in step (1), 0.3MPa compressed air is used to purge the outer surface of the SCR denitration catalytic filter element, and then 0.5MPa compressed air is used to clean the catalytic filter element from the inside Perform multiple backflushing to the outside; in step (2), soak the catalytic filter element in a dilute hydrochloric acid solution with a pH of 6 for 1 hour, and then use hot air at 105°C to dry the catalytic filter element for 4 hours; step (3) activity The concentration of oxalic acid in the liquid is 150mg / L, the concentration of ammonium metavanadate is 60mol / L, the concentration of ammonium metatungstate is 40mol / L, and catalytic filter element is soaked 3h in this mixed aqueous solution; In step (4), will The impregnated catalytic filter elements were baked at 450°C for 2 hours.
[0024] After the SCR denitrification catalytic filter element is treated by the regeneration method in this embod...
PUM
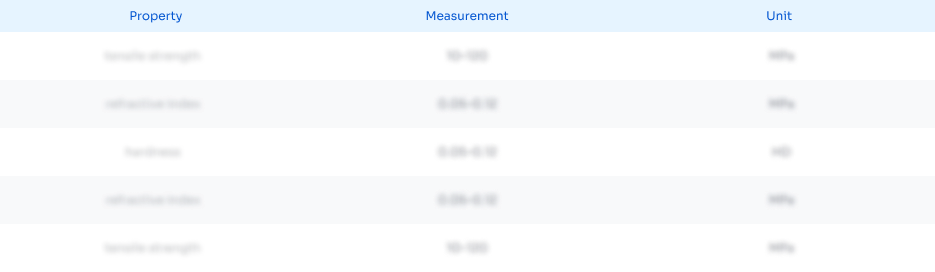
Abstract
Description
Claims
Application Information

- Generate Ideas
- Intellectual Property
- Life Sciences
- Materials
- Tech Scout
- Unparalleled Data Quality
- Higher Quality Content
- 60% Fewer Hallucinations
Browse by: Latest US Patents, China's latest patents, Technical Efficacy Thesaurus, Application Domain, Technology Topic, Popular Technical Reports.
© 2025 PatSnap. All rights reserved.Legal|Privacy policy|Modern Slavery Act Transparency Statement|Sitemap|About US| Contact US: help@patsnap.com