Method for the surface treatment of a workpiece
A workpiece surface and surface treatment technology, applied in the direction of cleaning methods using gas flow, heat treatment furnaces, heat treatment equipment, etc., can solve the problem that the blower cannot generate directional compressed airflow, and achieve the effect of reducing environmental and health hazards
- Summary
- Abstract
- Description
- Claims
- Application Information
AI Technical Summary
Problems solved by technology
Method used
Image
Examples
Embodiment Construction
[0025] exist figure 1In , a first version of a device 1 for carrying out the method according to the invention is shown. The device 1 contains a plurality of workstations in which workpieces 2 can be processed or processed one after the other. figure 1 The workpieces 2 involved in the plant 1 shown in are metal sheets or sheets which pass through the plant 1 in the direction of the arrow. exist figure 1 The plant 1 shown in FIG. 1 has a device 3 for cold forming a workpiece 2 as a first work station. The device 3 can be a press in which the workpiece 2 is plastically deformed. The deformed workpiece 2 then enters the furnace 4 as the next station of the plant 1 . exist figure 1 The furnace 4 shown in is a roller hearth furnace in which the deformed workpiece 2 is transported on rollers 5 and heated. Instead of such a roller hearth furnace, it is also possible to install a batch furnace with the workpieces 2 arranged in layers, as is known from DE 10 2010 043 229 A1.
[...
PUM
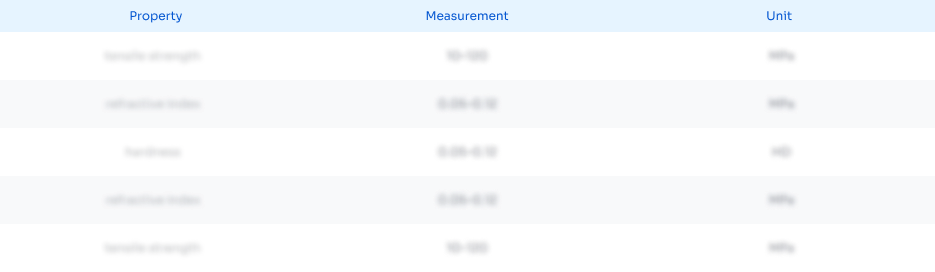
Abstract
Description
Claims
Application Information

- Generate Ideas
- Intellectual Property
- Life Sciences
- Materials
- Tech Scout
- Unparalleled Data Quality
- Higher Quality Content
- 60% Fewer Hallucinations
Browse by: Latest US Patents, China's latest patents, Technical Efficacy Thesaurus, Application Domain, Technology Topic, Popular Technical Reports.
© 2025 PatSnap. All rights reserved.Legal|Privacy policy|Modern Slavery Act Transparency Statement|Sitemap|About US| Contact US: help@patsnap.com