Modified anti-tear rubber
A tear-resistant and rubber technology, applied in the field of improved tear-resistant rubber, can solve the problems of scrapped rubber parts, safety accidents, and easy tearing of rubber materials, and achieve good compression resistance, good tear resistance, and good The effect of toughness and strength
- Summary
- Abstract
- Description
- Claims
- Application Information
AI Technical Summary
Problems solved by technology
Method used
Examples
Embodiment 1
[0008] An improved tear-resistant rubber, which is made of the following raw materials in parts by weight:
[0009] 9 parts of stearic acid, 4 parts of styrene-butadiene rubber, 15 parts of neoprene rubber, 6 parts of N115 reinforcing carbon black, 2 parts of dispersant, 14 parts of tetrapropylene fluorine rubber, 7 parts of magnesium stearate, 3 parts of acrylate copolymer 10 parts of epoxidized natural rubber, 1 part of sulfur, 10 parts of zinc diethyldithiocarbamate, 4 parts of sodium stearate, 1 part of plaster ash, 1 part of antifungal agent, and 13 parts of nitrile rubber.
Embodiment 2
[0011] An improved tear-resistant rubber, which is made of the following raw materials in parts by weight:
[0012] 11 parts of stearic acid, 8 parts of styrene-butadiene rubber, 21 parts of neoprene rubber, 10 parts of N115 reinforcing carbon black, 5 parts of dispersant, 20 parts of tetrapropylene fluororubber, 10 parts of magnesium stearate, 10 parts of acrylate copolymer 16 parts of epoxidized natural rubber, 5 parts of sulfur, 16 parts of zinc diethyldithiocarbamate, 7 parts of sodium stearate, 3 parts of plaster ash, 3 parts of antifungal agent, and 20 parts of nitrile rubber.
PUM
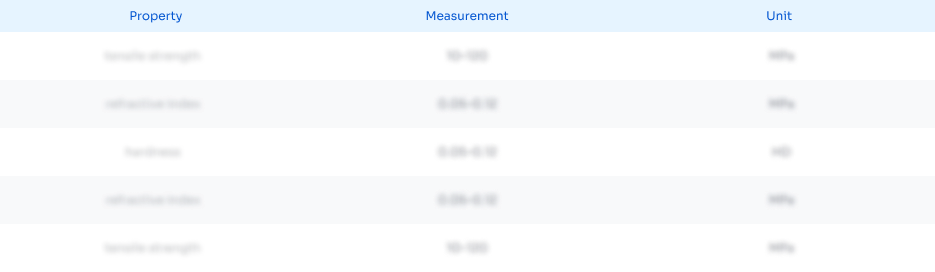
Abstract
Description
Claims
Application Information

- R&D Engineer
- R&D Manager
- IP Professional
- Industry Leading Data Capabilities
- Powerful AI technology
- Patent DNA Extraction
Browse by: Latest US Patents, China's latest patents, Technical Efficacy Thesaurus, Application Domain, Technology Topic, Popular Technical Reports.
© 2024 PatSnap. All rights reserved.Legal|Privacy policy|Modern Slavery Act Transparency Statement|Sitemap|About US| Contact US: help@patsnap.com