Die-casting die capable of secondarily laterally pulling core
A die-casting mold and lateral core-pulling technology, which is applied in the field of molds, can solve problems such as product packaging mold, bending deformation, product bending deformation, etc., and achieve the effect of improving production efficiency
- Summary
- Abstract
- Description
- Claims
- Application Information
AI Technical Summary
Problems solved by technology
Method used
Image
Examples
Embodiment Construction
[0022] The present invention will be further described below in conjunction with the accompanying drawings and specific embodiments.
[0023] Such as figure 1 As shown, a die-casting mold capable of secondary lateral core pulling is suitable for forming products with lateral holes and radial blind holes in the lateral holes; at the same time, it can also be formed with Products with openings or concave cavities, or products with close molding forces on the upper and lower sides of the parting surface. It specifically includes an upper mold 1 with a pouring system, and a lower mold 2 with an ejection mechanism. The upper mold has a lateral core-pulling hole 21, and a hole for forming a lateral hole and a radial blind hole is arranged in the lateral core-pulling hole. The main core 20 is connected with a driving cylinder 30 . For the sake of explanation, we refer to the mold splitting and mold closing directions of the upper and lower molds as the longitudinal direction of the...
PUM
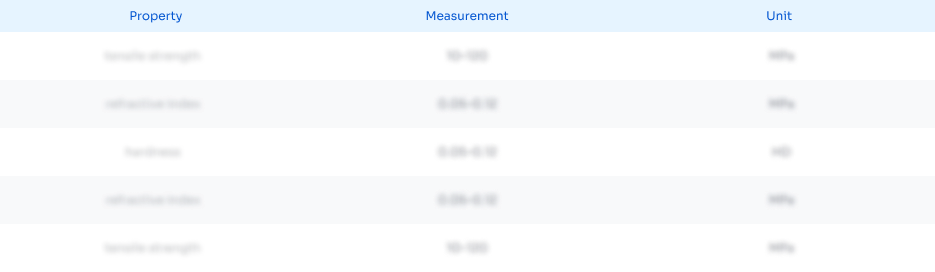
Abstract
Description
Claims
Application Information

- R&D
- Intellectual Property
- Life Sciences
- Materials
- Tech Scout
- Unparalleled Data Quality
- Higher Quality Content
- 60% Fewer Hallucinations
Browse by: Latest US Patents, China's latest patents, Technical Efficacy Thesaurus, Application Domain, Technology Topic, Popular Technical Reports.
© 2025 PatSnap. All rights reserved.Legal|Privacy policy|Modern Slavery Act Transparency Statement|Sitemap|About US| Contact US: help@patsnap.com