Prediction method of crack propagation life of aircraft body
A technology of crack extension life and aircraft body, applied in the direction of applying repeated force/pulsation force to test the strength of materials, etc., can solve the problems of complex calculation process, long time consumption, and increased cumulative error
- Summary
- Abstract
- Description
- Claims
- Application Information
AI Technical Summary
Problems solved by technology
Method used
Image
Examples
Embodiment Construction
[0054] The technical solutions of the present invention will be further described below in conjunction with the accompanying drawings and through specific implementation methods.
[0055] Such as figure 1 Shown is the aircraft body crack growth life prediction method in the present invention, comprising the following steps: Step A: Obtain the random load spectrum in the aircraft flight according to the actual flight conditions of the aircraft;
[0056] Step B: Divide the random load spectrum obtained in step A into several sections, use the rainflow counting method to count rainflow for each section, and perform constant amplitude for each section, so that each section is approximated as a block load spectrum;
[0057] Step C: use the load spectrum of each block obtained in step B to perform a fatigue test, and obtain the stress-life curve under the state where the stress ratio is R;
[0058] Step D: According to Miners cumulative damage theory and the stress-life curve obtai...
PUM
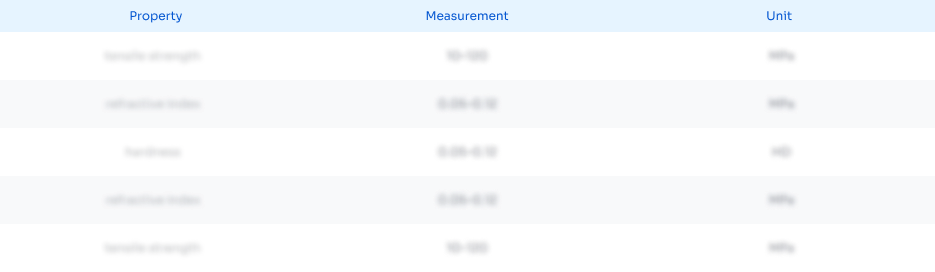
Abstract
Description
Claims
Application Information

- R&D
- Intellectual Property
- Life Sciences
- Materials
- Tech Scout
- Unparalleled Data Quality
- Higher Quality Content
- 60% Fewer Hallucinations
Browse by: Latest US Patents, China's latest patents, Technical Efficacy Thesaurus, Application Domain, Technology Topic, Popular Technical Reports.
© 2025 PatSnap. All rights reserved.Legal|Privacy policy|Modern Slavery Act Transparency Statement|Sitemap|About US| Contact US: help@patsnap.com