An energy-saving tunnel kiln
A tunnel kiln, energy-saving technology, applied in the direction of furnace type, furnace, lighting and heating equipment, etc., can solve the problem of affecting production cost and product quality, unable to achieve temperature adjustment, pressure adjustment effect, unreasonable design of coal feeding structure, etc. problem, to achieve the effect of saving labor input, setting reasonable heat insulation structure, and improving the effect of preheating
- Summary
- Abstract
- Description
- Claims
- Application Information
AI Technical Summary
Problems solved by technology
Method used
Image
Examples
Embodiment Construction
[0033] The present invention will be further described in detail below in conjunction with the accompanying drawings and examples. The following examples are explanations of the present invention and the present invention is not limited to the following examples.
[0034] see Figure 1-Figure 16 The energy-saving tunnel kiln in this embodiment includes a kiln body extending laterally and a kiln car running in the kiln body. The kiln body includes a kiln roof, a kiln wall and a working channel 1, and the working channel 1 sequentially includes an inlet in the direction of extension. Section L1, preheating section L2, roasting section L3, heat preservation section L4 and cooling section L5, the kiln wall includes a wall high platform 21 for fixing on the foundation, the wall high platform 21 is made of rubble bricks, and the wall A cushion layer 22 formed by pouring concrete is arranged on the body height platform 21 .
[0035]The first wall layer 23, the second wall layer 24, ...
PUM
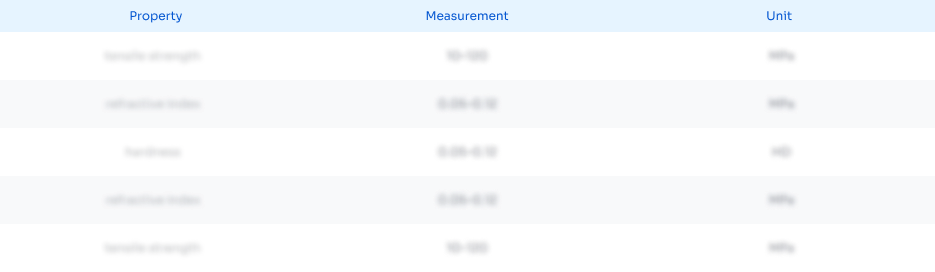
Abstract
Description
Claims
Application Information

- Generate Ideas
- Intellectual Property
- Life Sciences
- Materials
- Tech Scout
- Unparalleled Data Quality
- Higher Quality Content
- 60% Fewer Hallucinations
Browse by: Latest US Patents, China's latest patents, Technical Efficacy Thesaurus, Application Domain, Technology Topic, Popular Technical Reports.
© 2025 PatSnap. All rights reserved.Legal|Privacy policy|Modern Slavery Act Transparency Statement|Sitemap|About US| Contact US: help@patsnap.com