Shaft seal auxiliary flushing system for centrifugal pump and axial flow pump
A technology for flushing systems and axial flow pumps, applied to parts, pumps, pump elements, etc. of pumping devices for elastic fluids, which can solve problems such as burnout, failure to provide a backup pump 2 seal flushing scheme, and increased friction
- Summary
- Abstract
- Description
- Claims
- Application Information
AI Technical Summary
Problems solved by technology
Method used
Image
Examples
Embodiment Construction
[0052] A centrifugal pump and an axial-flow pump auxiliary flushing system for shaft seals of the present invention will be described in detail below with reference to the embodiments and the accompanying drawings.
[0053] A shaft seal auxiliary flushing system of a centrifugal pump and an axial flow pump of the present invention is in such as figure 1 , figure 2 What is realized on the basis of the prior art shown is that the washing systems of the main operating pump and the standby pump of the prior art are connected in parallel to realize. A shaft seal auxiliary flushing system of a centrifugal pump and an axial flow pump of the present invention, specifically as image 3 , Figure 4 As shown, it includes: the main operating pump 1 and the backup pump 2 respectively provided with the same shaft seal flushing system, the shaft seal flushing system of the main operating pump 1 and the shaft seal flushing system of the backup pump 2 are connected in parallel to form a mut...
PUM
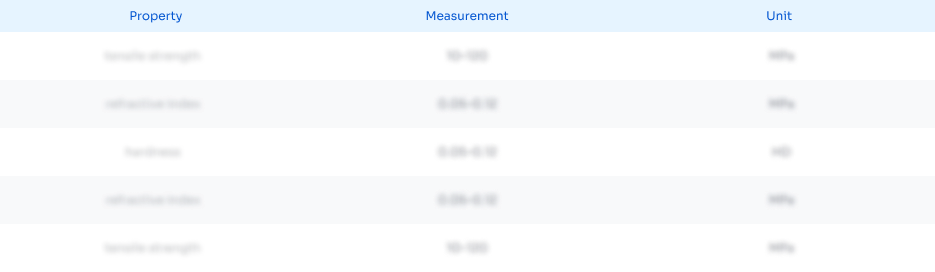
Abstract
Description
Claims
Application Information

- Generate Ideas
- Intellectual Property
- Life Sciences
- Materials
- Tech Scout
- Unparalleled Data Quality
- Higher Quality Content
- 60% Fewer Hallucinations
Browse by: Latest US Patents, China's latest patents, Technical Efficacy Thesaurus, Application Domain, Technology Topic, Popular Technical Reports.
© 2025 PatSnap. All rights reserved.Legal|Privacy policy|Modern Slavery Act Transparency Statement|Sitemap|About US| Contact US: help@patsnap.com