A device for friction welding phase control
A phase control and friction welding technology, applied in the field of friction welding, can solve the problems of easy damage to the motor and affect the welding quality, achieve uniform deceleration, improve stability, and avoid impact.
- Summary
- Abstract
- Description
- Claims
- Application Information
AI Technical Summary
Problems solved by technology
Method used
Image
Examples
Embodiment 1
[0029] Such as image 3 As shown, the device for friction welding phase control in this embodiment includes a control unit 20, a positioning unit 22, a positioning position unit 23, and a steel jaw clamp spindle motor 21. The control unit 20 is connected to the positioning unit 22 for sending positioning instructions to the positioning unit 22. The positioning unit 22 is respectively connected with the control unit 20 and the steel jaw clamp spindle motor 21 for controlling the steel jaw clamp spindle motor 21. For example, the positioning unit 22 controls the torque and the torque of the steel jaw clamp spindle motor 21 with output torque and speed signals. Rotation speed; the positioning unit 22 is also connected to the positioning unit 23, the positioning unit 23 periodically feedbacks a signal to the positioning unit 22, for example, every time the steel claw 11 rotates one revolution, the positioning unit 23 feedbacks a signal to the positioning unit 22; After receiving th...
Embodiment 2
[0036] Such as Figure 5 As shown, the device for friction welding phase control in this embodiment further includes a steel claw information unit 24 and an aluminum guide rod information unit 25.
[0037] The steel claw information unit 24 is respectively connected to the control unit 20 and the rear end of the reducer of the steel claw clamp spindle motor 21. The steel claw information unit 24 is used to collect the current position and speed information of the steel claw 11 and feed the information back to the control unit 20 , The control unit 20 calculates the number of turns of the steel claw 11 and the specific angle of the current circle where the steel claw 11 is located according to the position and speed information of the steel claw 11, so the control unit 20 first detects the steel before sending the positioning instruction to the positioning unit 22 The position information of the claw 11 to ensure that the steel claw 11 is in the same position before sending the pos...
Embodiment 3
[0040] Such as Image 6 As shown, the device for friction welding phase control in this embodiment further includes a speed feedback unit 26, which is respectively connected to the positioning unit 22 and the front end of the speed reducer of the steel jaw clamp spindle motor 21. The speed feedback unit 26 is used to collect the output speed of the positioning unit 22 and feedback the speed information to the positioning unit 22, so the speed feedback unit 26 and the positioning unit 22 construct a speed feedback closed loop, which improves the output accuracy of the positioning unit 22 and can assist in improving control. The positioning accuracy of the steel jaw clamp spindle motor 21. Among them, the speed feedback unit 26 is an incremental encoder.
[0041] The phase control accuracy of the anode conductive device obtained by using the present invention can be verified by the following measurement experiments:
[0042] 1. The experiment object is: when the aluminum guide rod ...
PUM
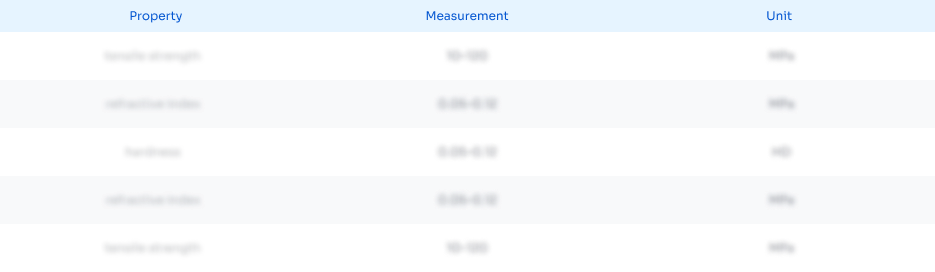
Abstract
Description
Claims
Application Information

- Generate Ideas
- Intellectual Property
- Life Sciences
- Materials
- Tech Scout
- Unparalleled Data Quality
- Higher Quality Content
- 60% Fewer Hallucinations
Browse by: Latest US Patents, China's latest patents, Technical Efficacy Thesaurus, Application Domain, Technology Topic, Popular Technical Reports.
© 2025 PatSnap. All rights reserved.Legal|Privacy policy|Modern Slavery Act Transparency Statement|Sitemap|About US| Contact US: help@patsnap.com