Catenary suspension linear ultrasound longitudinal vibration amplitude-change bar with hole formed in axial direction of output end
A horn and output technology, applied in the field of mechanical vibration, can solve the problems of shortening the service life of the transducer, increasing the input electric power of the transducer, limited amplitude amplification factor, etc., to achieve the effect of improving work efficiency
- Summary
- Abstract
- Description
- Claims
- Application Information
AI Technical Summary
Problems solved by technology
Method used
Image
Examples
Embodiment 1
[0017] exist figure 1 Among them, the catenary-shaped ultrasonic longitudinal vibration horn with an axial opening at the output end of the present invention is composed of the horn 1 . In this example, the two ends of the horn 1 are parallel planes perpendicular to the center line, and the side is a rod-shaped body with a hyperbolic cosine rotation surface. The geometric shape of the side is a curve in the rectangular coordinate system
[0018] y=(d / 2)chγ(L-x), where γ = 1 L arcch ( D / d )
[0019] is the rotating surface formed by the generatrix and the x-axis is the rotation axis, 0≤x≤length L of the horn, where y is the radius of the cross-section at the coordinate x, and D is the diameter of the large end of the horn 1. When in use, change The large end of the horn 1 is connected to the ultrasonic transducer, d is the diame...
Embodiment 2
[0022] In this example, the two ends of the horn 1 are parallel planes perpendicular to the center line, and the side is a rod-shaped body with a hyperbolic cosine rotation surface. The geometric shape of the side is a curve in the rectangular coordinate system
[0023] y=(d / 2)chγ(L-x), where γ = 1 L arcch ( D / d )
[0024] is the rotating surface formed by the generatrix and the x-axis is the rotation axis, 0≤x≤length L of the horn, where y is the radius of the section at the coordinate x, D is the diameter of the large end of the horn 1, and the length of the horn 1 The big end is the input and the little end is the output. The horn length L, the diameter D of the large end of the horn 1, the geometrical dimensions of the diameter d of the small end of the horn 1, and the materials used in this embodiment are the same as in Exa...
Embodiment 3
[0026] In this example, the two ends of the horn 1 are parallel planes perpendicular to the center line, and the side is a rod-shaped body with a hyperbolic cosine rotation surface. The geometric shape of the side is a curve in the rectangular coordinate system
[0027] y=(d / 2)chγ(L-x), where γ = 1 L arcch ( D / d )
[0028] is the rotating surface formed by the generatrix and the x-axis is the rotation axis, 0≤x≤length L of the horn, where y is the radius of the section at the coordinate x, D is the diameter of the large end of the horn 1, and the length of the horn 1 The big end is the input and the little end is the output. The horn length L, the diameter D of the large end of the horn 1, the geometrical dimensions of the diameter d of the small end of the horn 1, and the materials used in this embodiment are the same as in Exa...
PUM
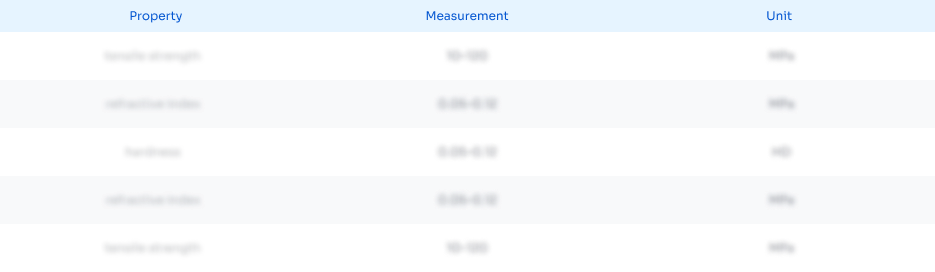
Abstract
Description
Claims
Application Information

- R&D
- Intellectual Property
- Life Sciences
- Materials
- Tech Scout
- Unparalleled Data Quality
- Higher Quality Content
- 60% Fewer Hallucinations
Browse by: Latest US Patents, China's latest patents, Technical Efficacy Thesaurus, Application Domain, Technology Topic, Popular Technical Reports.
© 2025 PatSnap. All rights reserved.Legal|Privacy policy|Modern Slavery Act Transparency Statement|Sitemap|About US| Contact US: help@patsnap.com