Oil baffle plate installation welding mode oil bottom case assembly
A technology for installing welding and oil baffles, applied in the direction of oil pan, engine components, lubricating parts, etc., can solve the problems of oil pan cracking, adding extra load, weakening the strength of oil pan, etc., and achieve the elimination of tensile stress Effect
- Summary
- Abstract
- Description
- Claims
- Application Information
AI Technical Summary
Problems solved by technology
Method used
Image
Examples
Embodiment 1
[0022] Embodiment 1, an oil pan assembly in which an oil baffle is installed and welded, which includes a pressure block, an oil pan body, and an oil baffle. The pressure block (11) is connected to the side of the oil sump body (14) by segmental welding to fix the oil baffle (12). The oil baffle (12) is clamped in the pressure block (11) of the oil pan body (14) and welded to the bottom surface of the oil pan body (14) in sections, and the oil baffle (12) ) is far away from the flange surface of the oil pan body (14) and is provided with a transverse reinforcing rib (13). The side of the oil pan body (14) is designed with a pressure block (11) for fixing the oil baffle (12). The pressure block (11) is used to clamp the oil baffle (12), and only the pressure block (11) The contact surface with the oil pan and the contact surface with the oil baffle (12) are not welded. The distance between the oil baffle plate (12) and the flange surface of the oil pan body (14) is relatively...
Embodiment 2
[0023] Example 2, such as Figure 1 to Figure 3 , which shows a schematic diagram of an oil pan assembly (1) according to a specific embodiment of the present invention.
[0024] like figure 1 and figure 2 As shown, an oil pan assembly in the way of installing and welding the oil baffle includes a pressure block (11), an oil baffle (12) and an oil pan body (14). The pressure block (11) is connected to the side of the oil pan body (14) by segmental welding, and only the contact side of the pressure block (11) and the oil pan body (14) is welded, and is in contact with the oil baffle plate (12) The edges are not welded. in image 3 The segmented welding area B is shown in , and it should be noted that the welding position is only an example, and those skilled in the art can determine the welding range according to different sizes of the oil baffle plate and the oil pan body. Since there is no welding at the contact edge between the briquetting block (11) and the oil baffle...
PUM
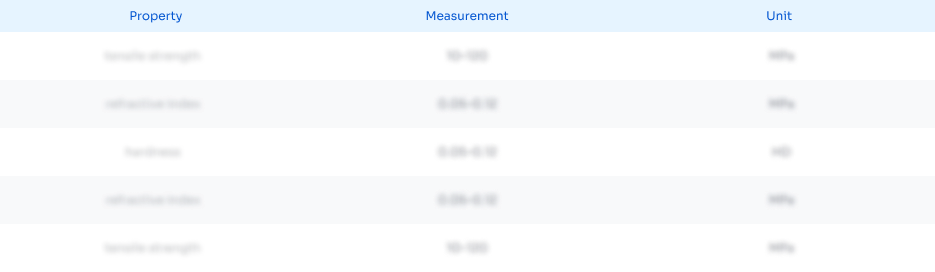
Abstract
Description
Claims
Application Information

- R&D
- Intellectual Property
- Life Sciences
- Materials
- Tech Scout
- Unparalleled Data Quality
- Higher Quality Content
- 60% Fewer Hallucinations
Browse by: Latest US Patents, China's latest patents, Technical Efficacy Thesaurus, Application Domain, Technology Topic, Popular Technical Reports.
© 2025 PatSnap. All rights reserved.Legal|Privacy policy|Modern Slavery Act Transparency Statement|Sitemap|About US| Contact US: help@patsnap.com