Quasi-zero stiffness vibration isolator connected with magnetic spring in parallel through spiral spring
A coil spring, magnetic spring technology, applied in the direction of spring/shock absorber, spring, shock absorber, etc., can solve the problems of small space size, difficulty, low natural frequency, etc., achieve low stress concentration, widen vibration isolation frequency band, Small footprint effect
- Summary
- Abstract
- Description
- Claims
- Application Information
AI Technical Summary
Problems solved by technology
Method used
Image
Examples
Embodiment Construction
[0022] The structural principle and working principle of the present invention will be further described in detail below in conjunction with the accompanying drawings.
[0023] Such as figure 1 , figure 2 with image 3 As shown, the present invention adopts a quasi-zero stiffness vibration isolator in parallel with a coil spring and a magnetic spring, including a coil spring 7, a first annular permanent magnet 15 arranged in the center cavity of the coil spring 7, and a The permanent magnet fixed cover 6 at the upper end of the body; the threaded section at one end of the quality support rod 1 with threaded sections at both ends passes through the threaded hole of the permanent magnet fixed cover 6, the central hole of the middle annular permanent magnet 15 and the central cavity of the coil spring 7 The central threaded hole at the bottom, the threaded hole of the middle permanent magnet fixing cover 6 and the central threaded hole at the bottom of the central cavity of th...
PUM
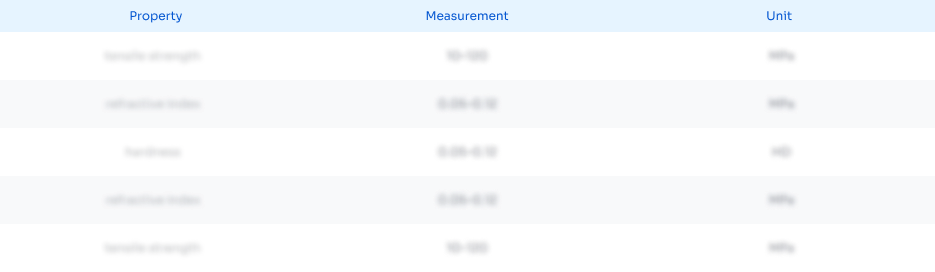
Abstract
Description
Claims
Application Information

- R&D
- Intellectual Property
- Life Sciences
- Materials
- Tech Scout
- Unparalleled Data Quality
- Higher Quality Content
- 60% Fewer Hallucinations
Browse by: Latest US Patents, China's latest patents, Technical Efficacy Thesaurus, Application Domain, Technology Topic, Popular Technical Reports.
© 2025 PatSnap. All rights reserved.Legal|Privacy policy|Modern Slavery Act Transparency Statement|Sitemap|About US| Contact US: help@patsnap.com