Mould material for high-strength forging and preparation method thereof
A mold material and high-strength technology, applied in the field of mold steel, can solve the problems of short life and cracks, and achieve the effect of prolonging the service life, strengthening the dispersion effect, and reducing the tendency of cracks.
- Summary
- Abstract
- Description
- Claims
- Application Information
AI Technical Summary
Problems solved by technology
Method used
Examples
Embodiment 1
[0028] A mold material for high-strength forging, its constituent elements and weight percentages are: C: 0.36%; Si: 0.50%; P≤0.035%; S≤0.010%; Cr: 7.6%; Mo: 4.7%; V : 2.6%; the rest is Fe.
[0029] The preparation method of the mold material for high-strength forging, the steps are:
[0030] 1) The raw materials are prepared according to the formula of C: 0.36%; Si: 0.50%; P≤0.035%; S≤0.010%; Cr: 7.6%; Mo: 4.7%; V: 2.6%; the rest is Fe to prepare the blank;
[0031] 2) Smelting Φ300 electroslag ingot according to the formula, 342mm length of the 190KG blanking material is put into the furnace for heating, the first step is to forge along the direction of the steel ingot to 600*200*200mm; the second step is to forge the direction of the steel ingot to 400*250* 220mm; the third step is to forge the steel ingot in the same direction to 700*225*125mm; to obtain the forged blank;
[0032] 3) Preheat the forged blank obtained in step 2) to 500°C, keep it warm for 40 minutes, then...
Embodiment 2
[0036] Same as Example 1, the difference is that the constituent elements and weight percentage of the test material are: C: 0.37%; Si: 0.40%; P≤0.035%; S≤0.010%; Cr: 7.1%; Mo: 5.0%; V: 2.1%; the rest is Fe; 1) Smelting Φ300 electroslag ingot according to the formula; 2) Blanking 210KG about 378mm long into the furnace for heating, the first step is to forge 600*215*215mm along the direction of the steel ingot, the second step, Forging the steel ingot with the same direction to 400*250*250mm, the third step is to forge the steel ingot with the same direction to Φ308*280*280mm; get the blank after forging; step 3) Preheat the blank to 450°C, hold it for 55min, and then heat it to 850°C, keep warm for 60min; then heat to 1050°C, keep warm for 50min, control the heating rate at 30°C / min for quenching, the quenching is water quenching, the water quenching adopts the quenching agent in the patent No. 201310350402.X embodiment 2; step 4) In the process, the workpiece was heated to 4...
Embodiment 3
[0038]Same as Example 1, the difference is that the constituent elements and weight percentage of the test material are: C: 0.38%; Si: 0.30%; P≤0.035%; S≤0.010%; Cr: 6.8%; Mo: 5.4%; V: 1.8%; the rest is Fe; 1) smelting Φ300 electroslag ingot according to the formula, 2) blanking 160KG about 288mm long into the furnace for heating, the first step is to forge 600*225*150mm along the direction of the steel ingot, the second step, Forge the steel ingot with the same direction to 400*300*160mm, the third step is to forge the steel ingot with the same direction to 555*255*125mm; get the blank after forging; step 3) Preheat the blank to 450°C, keep it warm for 70min, and then heat it to 860 ℃, heat preservation 40min; Then be heated to 1030 ℃, heat preservation 60min, heating rate is controlled at 26 ℃ / min; Quenching is water quenching, and water quenching adopts the quenchant in the patent No. 201310350402.X embodiment 2; Step 4) will The workpiece was heated to 550°C, held for 180 ...
PUM
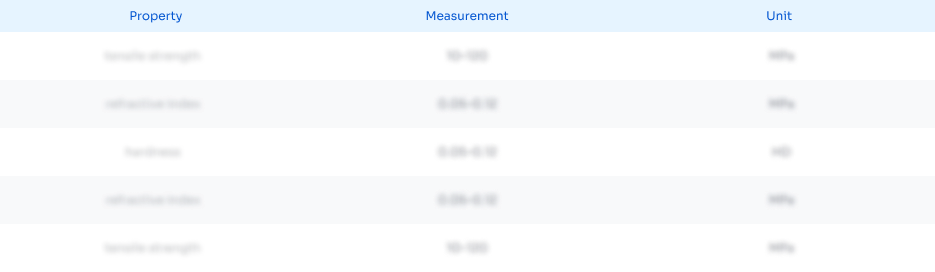
Abstract
Description
Claims
Application Information

- R&D
- Intellectual Property
- Life Sciences
- Materials
- Tech Scout
- Unparalleled Data Quality
- Higher Quality Content
- 60% Fewer Hallucinations
Browse by: Latest US Patents, China's latest patents, Technical Efficacy Thesaurus, Application Domain, Technology Topic, Popular Technical Reports.
© 2025 PatSnap. All rights reserved.Legal|Privacy policy|Modern Slavery Act Transparency Statement|Sitemap|About US| Contact US: help@patsnap.com