Method for filling and synthetizing full waterborne polyurethane base leather through nano attapulgite
A polyurethane leather bass and nano attapulgite technology, applied in textiles and papermaking, etc., can solve the problems of insufficient nano reinforcement performance, low production efficiency, dispersion and dissociation, etc., and achieve easy mass production and stable performance. , Good thickening effect
- Summary
- Abstract
- Description
- Claims
- Application Information
AI Technical Summary
Problems solved by technology
Method used
Examples
Embodiment 1
[0018] Example 1: Select non-woven fabric as the base fabric and impregnate it in 15wt% NaCl aqueous solution. After impregnation, the liquid carrying rate of the base fabric is 35wt%, and the coating amount is 800g / m 3 ;Dry and iron the impregnated base cloth, surface calendering treatment; 15 grams of montmorillonite attapulgite with attapulgite content of 45wt% and montmorillonite content of 40wt% is pulverized to more than 200 mesh, and soaked with 100wt% water for 24h , extruded 5 times on the roll, after aging for 12 hours, add 100 grams of anionic water-based polyurethane 8000rpm high-speed pre-dispersion for 30min, then add 7 grams of sodium stearate, 4 grams of stearic acid amine, 4 grams of water-based pigment paste 6000rpm high-speed Stir for 20 minutes to make a water-based polyurethane synthetic leather slurry; soak the pretreated base cloth in the water-based polyurethane synthetic leather slurry, scrape the surface, and dry to prepare a water-based polyurethane s...
Embodiment 2
[0019] Example 2: Select non-woven fabric as the base fabric, impregnate it in 5wt% NaCl aqueous solution, the liquid carrying rate of the base fabric after impregnation is 15wt%, and the coating amount is 400g / m 3 ; Dry and iron the impregnated base cloth, surface calendering treatment; 12 grams of dolomite attapulgite with attapulgite content of 25wt% and dolomite content of 60wt% is pulverized to more than 250 mesh, and soaked with 50wt% water for 12h. Roll extrusion 3 times, after aging for 4 hours, add 100 grams of anionic water-based polyurethane 10000rpm high-speed pre-dispersion for 30 minutes, then add 3 grams of sodium dodecylbenzenesulfonate, 2 grams of stearic acid amine, 1 gram of water-based pigment paste Stir at a high speed of 8000rpm for 20 minutes to make a water-based polyurethane synthetic leather slurry; dip the pretreated base cloth into the water-based polyurethane synthetic leather slurry, scrape the surface, and dry it to make a water-based polyurethane...
Embodiment 3
[0020] Embodiment 3: select non-woven fabric as the base cloth, impregnate it in 10wt% NaCl aqueous solution, after impregnating, the liquid carrying rate of the base cloth is 25wt%, and the coating amount is 600g / m 3 ; Dry and flatten the impregnated base cloth, and perform surface calendering treatment; 8 grams of high-viscosity attapulgite with a content of attapulgite of 70wt% is crushed to more than 300 mesh, soaked with 75wt% water for 18 hours, and squeezed 4 times , after aging for 8 hours, add 100 grams of anionic water-based polyurethane 8000rpm high-speed pre-dispersion for 30 minutes, then add 5 grams of sodium stearate, 3 grams of sodium succinate, 2.5 grams of water-based pigment paste 6000rpm high-speed stirring for 20 minutes to make water-based polyurethane synthetic leather Slurry: immersing the pretreated base cloth in the water-based polyurethane synthetic leather slurry, smoothing the surface, and drying to obtain the water-based polyurethane synthetic leat...
PUM
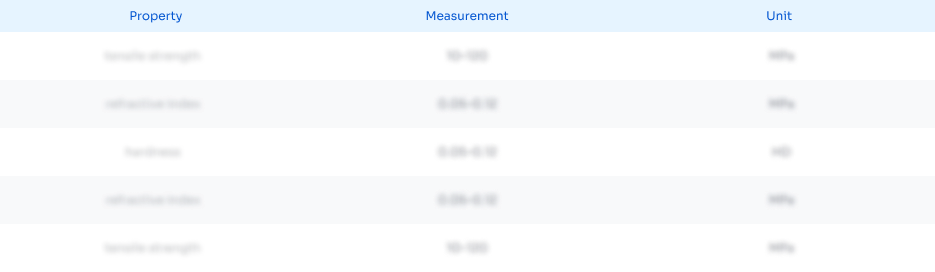
Abstract
Description
Claims
Application Information

- Generate Ideas
- Intellectual Property
- Life Sciences
- Materials
- Tech Scout
- Unparalleled Data Quality
- Higher Quality Content
- 60% Fewer Hallucinations
Browse by: Latest US Patents, China's latest patents, Technical Efficacy Thesaurus, Application Domain, Technology Topic, Popular Technical Reports.
© 2025 PatSnap. All rights reserved.Legal|Privacy policy|Modern Slavery Act Transparency Statement|Sitemap|About US| Contact US: help@patsnap.com