A Welding Process for Suppressing Discharge at the Tip of Solder Joints
A cutting-edge discharge and process technology, applied in manufacturing tools, welding equipment, metal processing, etc., can solve problems such as product quality not meeting requirements, inconsistent solder joint tip forms, circuit short circuits, etc., to eliminate tip phenomenon and eliminate tip discharge. , the effect of improving product quality
- Summary
- Abstract
- Description
- Claims
- Application Information
AI Technical Summary
Problems solved by technology
Method used
Image
Examples
Embodiment Construction
[0051] As shown in Figure 1, the present invention relates to a welding process for suppressing discharge at the tip of solder joints, which includes:
[0052] A. Through-hole component insertion:
[0053] A1) Confirm the product model, confirm the component number, confirm the component insertion method, vertical insertion, horizontal insertion, high insertion, and whether to use spacer columns, etc., to ensure the length of the component pin formation;
[0054] A2) Adjust the scale of the machine or self-made fixture;
[0055] A3) Take a component, shape it according to the requirements, insert the component into the corresponding bit number of the corresponding product board, and use a vernier caliper to check whether the length of the part of the leaking board meets the process requirements;
[0056] A4) Repeatedly adjust the scale of the machine or self-made fixtures to make the shape and length of the component pins meet the process requirements;
[0057] A5) Start bat...
PUM
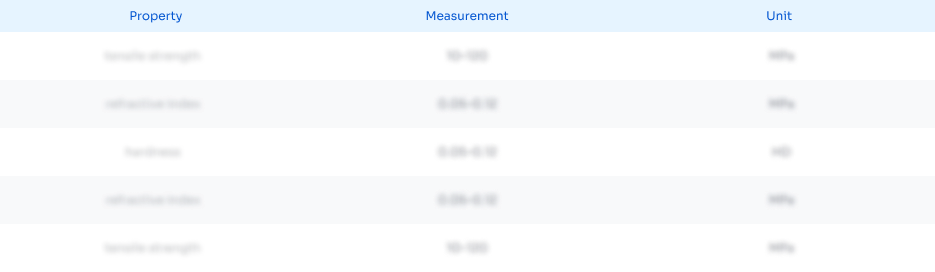
Abstract
Description
Claims
Application Information

- R&D
- Intellectual Property
- Life Sciences
- Materials
- Tech Scout
- Unparalleled Data Quality
- Higher Quality Content
- 60% Fewer Hallucinations
Browse by: Latest US Patents, China's latest patents, Technical Efficacy Thesaurus, Application Domain, Technology Topic, Popular Technical Reports.
© 2025 PatSnap. All rights reserved.Legal|Privacy policy|Modern Slavery Act Transparency Statement|Sitemap|About US| Contact US: help@patsnap.com