Composite spring buffer device for preventing bumping in oil tank
The technology of a buffer device and a composite spring is applied in the field of the composite spring buffer device, which can solve problems such as bumps on the surface of workpieces, and achieve the effects of easy maintenance, solving the collision of workpieces with each other, and facilitating maintenance.
- Summary
- Abstract
- Description
- Claims
- Application Information
AI Technical Summary
Problems solved by technology
Method used
Image
Examples
Embodiment Construction
[0017] The present invention will be described in detail below in conjunction with accompanying drawing: Figures 1 to 3 As shown, in the anti-bump composite spring buffer device in the oil tank described in the present invention, the buffer device assembly 4 is located between the drop hopper 2 and the oil tank lifting mesh belt 3, and the buffer device assembly 4 is composed of a spring 5 , material receiving buffer plate 6, material receiving mesh belt 7, steel wire rope 8, guide rail 9, material receiving plate fixing frame 10, spring fixed bottom plate 11 and spring fixing seat 12; the top of the material receiving buffer plate 6 is fastened Parts are fixed on the top of the material receiving plate fixing frame 10, and the bottom of the material receiving buffer plate 6 is equipped with a spring 5, a spring holder 12 and a spring fixed base plate 11, and the spring 5 is located between the material receiving buffer plate 6 and the spring fixed base plate 11, The spring f...
PUM
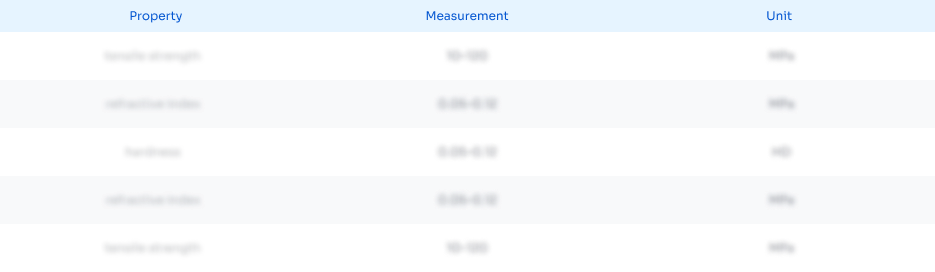
Abstract
Description
Claims
Application Information

- R&D Engineer
- R&D Manager
- IP Professional
- Industry Leading Data Capabilities
- Powerful AI technology
- Patent DNA Extraction
Browse by: Latest US Patents, China's latest patents, Technical Efficacy Thesaurus, Application Domain, Technology Topic, Popular Technical Reports.
© 2024 PatSnap. All rights reserved.Legal|Privacy policy|Modern Slavery Act Transparency Statement|Sitemap|About US| Contact US: help@patsnap.com