Method for forming mems acceleration sensor
A dielectric layer and substrate technology, applied in the direction of measuring acceleration, velocity/acceleration/impact measurement, instruments, etc., can solve the problems of etchant residue, affecting the performance of acceleration sensor, and cannot be removed cleanly, so as to achieve the effect of improving performance
- Summary
- Abstract
- Description
- Claims
- Application Information
AI Technical Summary
Problems solved by technology
Method used
Image
Examples
no. 1 example
[0053] refer to Figure 5 , a substrate 100 is provided, and a control circuit (not shown in the figure) is formed on the substrate 100 . The control circuit is used for receiving electrical signals and converting the electrical signals into inertial force, which is also called acceleration force, which refers to the force acting on the object during the acceleration process.
[0054] In a specific embodiment, the control circuit includes device structures such as transistors. The substrate 100 may be a silicon substrate, a germanium substrate, a silicon-on-insulator substrate, etc.; or the material of the substrate 100 may also include other materials, such as group III-V compounds such as gallium arsenide. Those skilled in the art can select the substrate as required, so the type of the substrate should not limit the protection scope of the present invention.
[0055] refer to Image 6 , a first dielectric layer 101 is formed on the substrate 100, the first dielectric lay...
no. 2 example
[0079] refer to Figure 12 , forming a second dielectric layer 302 on the first dielectric layer 301, the second dielectric layer 302 covering the first dielectric layer 301 and the lower plate 304;
[0080] refer to Figure 13 , the first dielectric layer 301 is patterned to form a groove 309, the groove 304 defines the position of the cavity, and the groove 309 exposes the lower plate 304;
[0081] refer to Figure 14 , in groove 309 (cf. Figure 13), an etch stop layer 310 and a third dielectric layer 303 on the etch stop layer 310 are formed, the etch stop layer 310 covers the bottom and sidewalls of the trench, and the third dielectric layer 303 fills the trench. The etching barrier layer 310 is used to protect the lower electrode plate 304 and prevent the lower electrode plate 304 from being damaged in the subsequent process of forming the cavity.
[0082] In a specific embodiment, the materials of the first dielectric layer 301 , the second dielectric layer 302 and ...
PUM
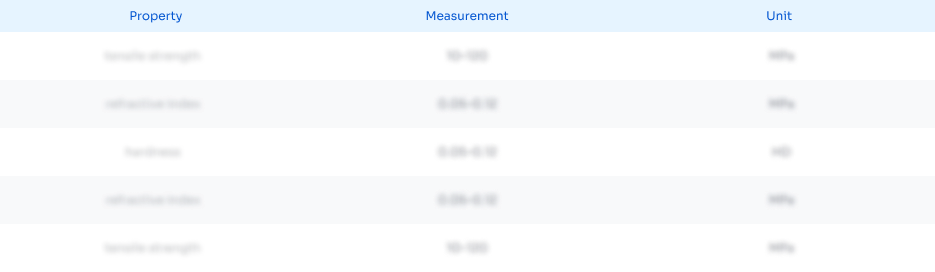
Abstract
Description
Claims
Application Information

- R&D Engineer
- R&D Manager
- IP Professional
- Industry Leading Data Capabilities
- Powerful AI technology
- Patent DNA Extraction
Browse by: Latest US Patents, China's latest patents, Technical Efficacy Thesaurus, Application Domain, Technology Topic, Popular Technical Reports.
© 2024 PatSnap. All rights reserved.Legal|Privacy policy|Modern Slavery Act Transparency Statement|Sitemap|About US| Contact US: help@patsnap.com