Tooth splicing machining method for machining herringbone gears
A processing method and technology of processing personnel, applied to components with teeth, belts/chains/gears, gear teeth, etc., can solve the problems of low processing efficiency, not suitable for mass production, and false shafts affecting the accuracy of gears, etc., to improve Accuracy, significant economic benefits, and easy-to-use effects
- Summary
- Abstract
- Description
- Claims
- Application Information
AI Technical Summary
Problems solved by technology
Method used
Image
Examples
Embodiment
[0031] Example: Taking the processing of a certain type of herringbone gear as an example, the gear parameters are: modulus M=5, number of teeth Z=73, pressure angle α=20°, helix angle β=11°30', helical direction: left-handed, right-handed 1 piece for each screw, displacement coefficient X=0.03, length of common normal line spanning 9 teeth During the processing, just pay attention that the keyway will not be processed temporarily. When the teeth are ground after heating, the common normal dimensions of the two paired gears will be ground to the same size, and the rest can be processed as ordinary helical gears. , The measurement results show that the tooth symmetry of the herringbone gear can reach within 0.03mm.
PUM
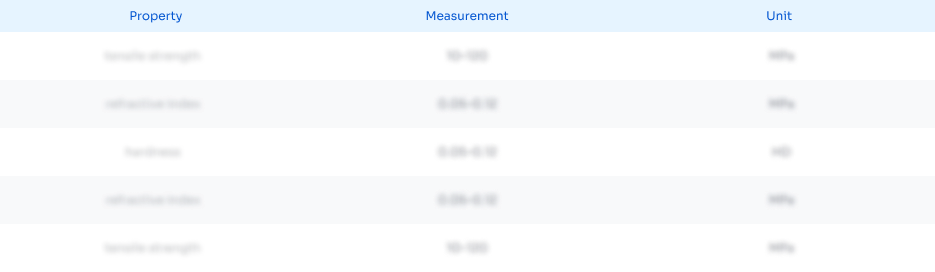
Abstract
Description
Claims
Application Information

- R&D Engineer
- R&D Manager
- IP Professional
- Industry Leading Data Capabilities
- Powerful AI technology
- Patent DNA Extraction
Browse by: Latest US Patents, China's latest patents, Technical Efficacy Thesaurus, Application Domain, Technology Topic, Popular Technical Reports.
© 2024 PatSnap. All rights reserved.Legal|Privacy policy|Modern Slavery Act Transparency Statement|Sitemap|About US| Contact US: help@patsnap.com