Method for conducting analog simulation on crank die forging process through computer aided engineering (CAE)
A computer-aided, simulation technology, applied in computing, special data processing applications, instruments, etc., can solve problems such as limited optimization, easy folding, and heavy workload, so as to reduce work difficulty, reduce forming load, and reduce work A large amount of effect
- Summary
- Abstract
- Description
- Claims
- Application Information
AI Technical Summary
Problems solved by technology
Method used
Image
Examples
Embodiment Construction
[0039] In order to make the measures, creative features, goals and effects achieved by the technology of the present invention easy to understand, the present invention will be further described below in conjunction with specific illustrations.
[0040] The invention provides a method for computer-aided engineering CAE simulation crankshaft die forging process, comprising the following steps:
[0041] Step 1, using the orthogonal experiment method, extracting the fillet of the parting surface of the pre-forging die cavity, the length, width and height ratio factors of the pre-forging die cavity and the final forging die cavity, forming four factors, and then establishing the factor level table, specifically As shown in Table 1:
[0042] Table I
[0043]
[0044] Step 2, according to the factor level table, draw such as figure 1 The crankshaft model shown;
[0045] Step 3, according to the crankshaft model samples of 16 groups of orthogonal schemes, proceed as follows f...
PUM
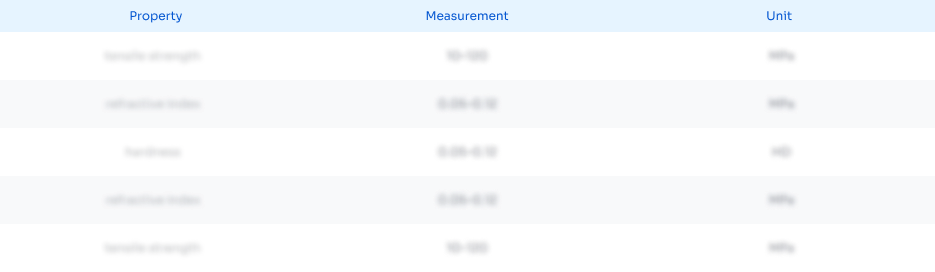
Abstract
Description
Claims
Application Information

- R&D
- Intellectual Property
- Life Sciences
- Materials
- Tech Scout
- Unparalleled Data Quality
- Higher Quality Content
- 60% Fewer Hallucinations
Browse by: Latest US Patents, China's latest patents, Technical Efficacy Thesaurus, Application Domain, Technology Topic, Popular Technical Reports.
© 2025 PatSnap. All rights reserved.Legal|Privacy policy|Modern Slavery Act Transparency Statement|Sitemap|About US| Contact US: help@patsnap.com