Multi-wire sawing method and multi-wire sawing machine
A multi-wire cutting machine and multi-wire cutting technology are applied to fine working devices, manufacturing tools, stone processing equipment, etc., which can solve the problems of fewer workpieces, difficult operation, and affecting cutting accuracy, and achieve processing quality and Improved processing accuracy, wide application range, and improved workpiece quality
- Summary
- Abstract
- Description
- Claims
- Application Information
AI Technical Summary
Problems solved by technology
Method used
Image
Examples
Embodiment 1
[0038] For specific embodiments of the present invention, refer to Figure 3 to Figure 6 , a multi-wire cutting machine, including four wire rollers (roller) 1, several cutting wires 2 arranged in parallel are wound on the wire rollers 1, and an upper workbench 3 and a lower workbench 4 are also included.
[0039]Wherein, the surface of each wire roller 1 is provided with an outer layer covered with polyurethane, and a plurality of grooves are arranged outside the polyurethane layer. And set the driving device (not shown) that the steel wire wound in the groove moves, and above-mentioned driving device is all prior art.
[0040] The upper workbench 3 is driven by a screw and a servo device, and can move in the up and down direction. Two parallel bosses 31 are formed below the upper workbench 3 and arranged at a certain distance. The bottom surface of each fixed column 31 is bonded with a Backing plate 5, in the present invention, the material of this backing plate is glass, a...
PUM
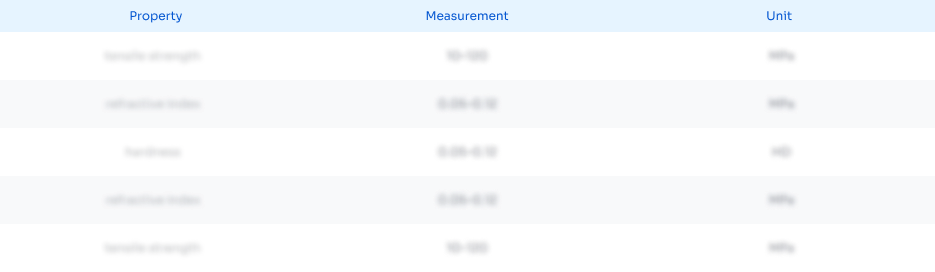
Abstract
Description
Claims
Application Information

- R&D Engineer
- R&D Manager
- IP Professional
- Industry Leading Data Capabilities
- Powerful AI technology
- Patent DNA Extraction
Browse by: Latest US Patents, China's latest patents, Technical Efficacy Thesaurus, Application Domain, Technology Topic, Popular Technical Reports.
© 2024 PatSnap. All rights reserved.Legal|Privacy policy|Modern Slavery Act Transparency Statement|Sitemap|About US| Contact US: help@patsnap.com