Turning technique for long spoke portion of integral impeller
A technology of integral impeller and process method, applied in the direction of turbines, mechanical equipment, etc., can solve the problems of high processing resistance, poor thermal conductivity, excessive size and technical conditions, etc., and achieve the effect of high processing quality and accurate processing dimensions.
- Summary
- Abstract
- Description
- Claims
- Application Information
AI Technical Summary
Problems solved by technology
Method used
Image
Examples
Embodiment Construction
[0013] Below in conjunction with accompanying drawing and specific embodiment the present invention will be described in further detail: as figure 1 Shown is a schematic diagram of the structure of the new fixture used in one embodiment of the present invention after it is matched with the parts.
[0014] In the past, ordinary structure fixtures were used, and secondary clamping and alignment processing was required for single-sided turning. The new fixture of the present invention includes a frame 1, and an auxiliary support block 3 is added to the spoke umbilicus of the integral impeller part 4, and an auxiliary support block 3 is added to the integral impeller part 4 An anti-hook compression block 2 is added to the outer edge of the long-radius plate. Bolts are arranged on the anti-hook compression block 2, and the anti-hook compression block 2 can be tightened by tightening the bolts to compress the long-radius plate. The outer edge can increase the processing rigidity of ...
PUM
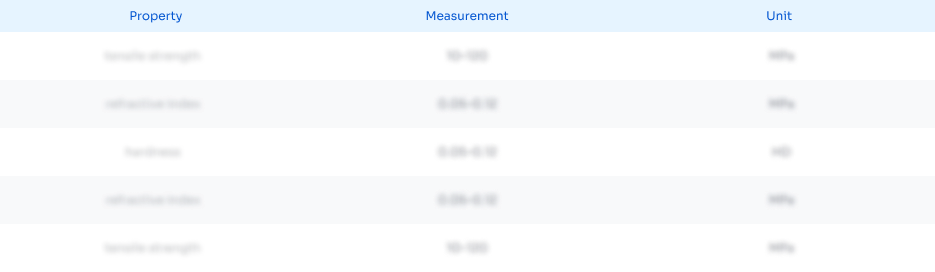
Abstract
Description
Claims
Application Information

- R&D Engineer
- R&D Manager
- IP Professional
- Industry Leading Data Capabilities
- Powerful AI technology
- Patent DNA Extraction
Browse by: Latest US Patents, China's latest patents, Technical Efficacy Thesaurus, Application Domain, Technology Topic, Popular Technical Reports.
© 2024 PatSnap. All rights reserved.Legal|Privacy policy|Modern Slavery Act Transparency Statement|Sitemap|About US| Contact US: help@patsnap.com