Oriented graphene/bismaleimide multilevel composite material and preparation method thereof
A technology of bismaleimide and composite material, applied in the field of oriented graphene/bismaleimide multi-layer composite material and preparation thereof
- Summary
- Abstract
- Description
- Claims
- Application Information
AI Technical Summary
Problems solved by technology
Method used
Image
Examples
specific Embodiment approach
[0025] Step 1: Graphene oxide with a mass fraction of 5 to 25 parts and FeCl with 40 to 100 parts 3 ·6H 2 O and 10-40 parts of FeCl 2 4H 2 Disperse O into 10,000-20,000 parts of deionized water, ultrasonically disperse at 100-300W for 10-30min, add 0.4mol / L NaOH aqueous solution to adjust pH=11, heat in 0.05-0.5T magnetic field, 50 After reacting at ~80°C for 2 hours, add 50-200 parts of hydrazine hydrate and raise the temperature to 98°C for 4 hours, filter with suction, wash, and dry in vacuum to obtain GNSFe3 o 4 .
[0026] Step 2: GNSFe with a mass fraction of 0.1 to 50 parts 3 o 4 , 0.1-50 parts of hyperbranched polysiloxane-modified graphene (for its preparation method, see invention patent ZL201210234077.6), 100 parts of diphenylmethane-type bismaleimide and 10-100 parts of diallyl Based on bisphenol A, heated to 130-160°C, melted, stirred evenly, poured into the mold, defoamed, and cured in a static magnetic field of 0.05-0.5T, the curing process was 150°C / 2h+180...
Embodiment 1
[0028] Step 1: the mass fraction is 5 parts of graphene oxide, 40 parts of FeCl 3 ·6H 2 O and 17 parts of FeCl 2 4H 2 Disperse O into 10000 parts of deionized water, ultrasonically disperse for 10 to 30 minutes at a power of 100 to 300 W, add 0.4 mol / L NaOH aqueous solution to adjust pH = 11, and heat in a 0.05 to 0.5 T magnetic field, 50 to 80 After reacting at ℃ for 2 hours, add 50-200 parts of hydrazine hydrate and raise the temperature to 98 ℃ for 4 hours, filter with suction, wash, and dry in vacuum to obtain GNSFe 3 o 4 .
[0029] Step 2: the mass fraction is 0.2 parts of GNSFe 3 o 4 , 0.1 part of hyperbranched polysiloxane-modified graphene, 100 parts of diphenylmethane type bismaleimide and 30 parts of diallyl bisphenol A, heated to 130-160 ° C, melted, stirred Evenly, pour it into the mold, defoam, put it in a static magnetic field of 0.05 ~ 0.5T to cure, the curing process is 150°C / 2h+180°C / 2h+220°C / 4h, then naturally cool, after demoulding, at 250 After post...
Embodiment 2
[0031] Step 1: the mass fraction is 10 parts of graphene oxide, 60 parts of FeCl 3 ·6H 2 O and 25 parts of FeCl 2 4H 2 Disperse O into 13000 parts of deionized water, ultrasonically disperse for 10 to 30 minutes at a power of 100 to 300 W, add 0.4 mol / L NaOH aqueous solution to adjust pH = 11, and heat in a 0.05 to 0.5 T magnetic field, 50 to 80 After reacting at ℃ for 2 hours, add 50-200 parts of hydrazine hydrate and raise the temperature to 98 ℃ for 4 hours, filter with suction, wash, and dry in vacuum to obtain GNSFe 3 o 4 .
[0032] Step 2: the mass fraction is 0.4 parts of GNSFe 3 o 4 , 0.2 parts of hyperbranched polysiloxane-modified graphene, 100 parts of diphenylmethane bismaleimide and 40 parts of diallyl bisphenol A, heated to 130-160 ° C, melted, stirred Evenly, pour it into the mold, defoam, put it in a static magnetic field of 0.05 ~ 0.5T to cure, the curing process is 150°C / 2h+180°C / 2h+220°C / 4h, then naturally cool, after demoulding, at 250 After post-tr...
PUM
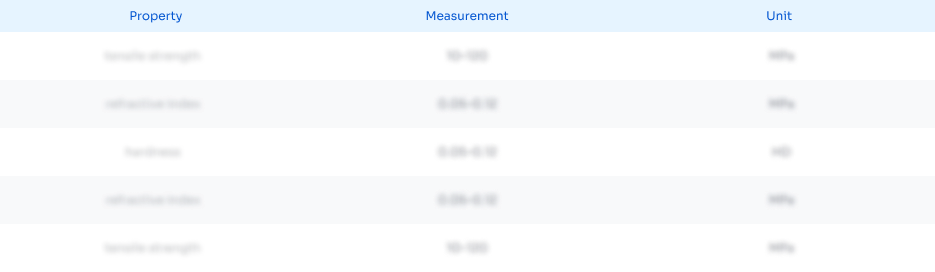
Abstract
Description
Claims
Application Information

- R&D
- Intellectual Property
- Life Sciences
- Materials
- Tech Scout
- Unparalleled Data Quality
- Higher Quality Content
- 60% Fewer Hallucinations
Browse by: Latest US Patents, China's latest patents, Technical Efficacy Thesaurus, Application Domain, Technology Topic, Popular Technical Reports.
© 2025 PatSnap. All rights reserved.Legal|Privacy policy|Modern Slavery Act Transparency Statement|Sitemap|About US| Contact US: help@patsnap.com