A Design Method of Hydraulic System Based on Multi-source Network
A technology of hydraulic system and design method, which is applied in the direction of mechanical equipment, fluid pressure actuators, servo motors, etc., and can solve problems such as high maintenance costs, increased internal leakage of hydraulic pumps, and poor speed characteristics of hydraulic cylinders or hydraulic motors. Achieve the effect of high energy utilization rate, high reliability and high reliability
- Summary
- Abstract
- Description
- Claims
- Application Information
AI Technical Summary
Problems solved by technology
Method used
Image
Examples
Embodiment Construction
[0023] Such as figure 2 and image 3 As shown, the present invention consists of 14 components, which can be divided into four modules: multi-source flow level, pressure classification module, function control valve module and multiple actuators. The multi-source flow stage includes fuel tank 1, motors 2.1, 2.2, 2.3, hydraulic pumps (first quantitative pump 4.1, second quantitative pump 4.2 and variable displacement pump 3), accumulators (low-pressure accumulator 10, medium-pressure accumulator device 9 and high-pressure accumulator 8), the first bypass unloading valve 7.1, the second bypass unloading valve 7.2, the first one-way valve 6.1, the second one-way valve 6.2, the third one-way valve 6.3; based on The idea of the network, all the hydraulic pumps inside the multi-source flow stage (including the first quantitative pump 4.1, the second quantitative pump 4.2 and the variable pump 3) must be connected to a check valve at the outlet, respectively the first check valve...
PUM
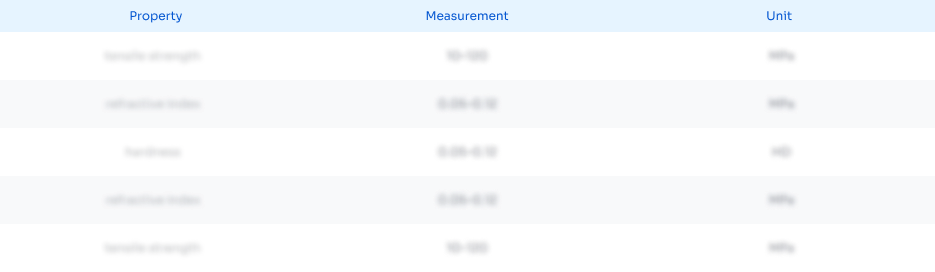
Abstract
Description
Claims
Application Information

- R&D
- Intellectual Property
- Life Sciences
- Materials
- Tech Scout
- Unparalleled Data Quality
- Higher Quality Content
- 60% Fewer Hallucinations
Browse by: Latest US Patents, China's latest patents, Technical Efficacy Thesaurus, Application Domain, Technology Topic, Popular Technical Reports.
© 2025 PatSnap. All rights reserved.Legal|Privacy policy|Modern Slavery Act Transparency Statement|Sitemap|About US| Contact US: help@patsnap.com