Method for stripping organic fluorine waterproof agent
A water repellent, organic fluorine technology, applied in textiles and papermaking, fiber processing, plant fibers, etc., can solve the problems of color difference defective cloth can not be repaired, can not achieve good peeling effect, etc., achieve excellent hydrophilic performance, Reproducible results
- Summary
- Abstract
- Description
- Claims
- Application Information
AI Technical Summary
Problems solved by technology
Method used
Image
Examples
Embodiment 1
[0024] Cotton thick twill gauze garment fabric after organic fluorine three-proof and non-ironing finishing, specification: 16SX12S / 108X56, stripping organic fluorine three-proof, including the following specific steps:
[0025] (1) Configure the working solution; the working solution contains 20g / L silicon spot stripping agent FORYL CPH, 10g / L caustic soda;
[0026] (2) Put the fabric that needs to be repaired into the working solution, and boil it for 45 minutes at 115°C;
[0027] (3) Wash with hot water at a temperature of 95°C for 10 minutes;
[0028] (4) Configure fresh working solution; containing 15g / L hydrophilic finishing agent KINDGER DF-C, 5g / L isopropanol;
[0029] (5) Place the fabric treated in step (3) in the fresh working solution prepared in step (4), and heat it up to 100°C for 30 minutes;
[0030] (6) Finally, wash with hot water above 90°C for 5-10 minutes.
[0031] The temperature of the step (3) is strictly controlled, and the repaired fabric can only ...
Embodiment 2
[0034] Cotton thick twill gauze garment fabric after organic fluorine three-proof and non-ironing finishing, specification: 16SX12S / 108X56, stripping organic fluorine three-proof, including the following specific steps:
[0035] (1) Configure the working solution; the working solution contains 15g / L silicon spot stripping agent FORYL CPH, 20g / L caustic soda;
[0036] (2) Put the fabric that needs to be repaired into the working solution, and boil it for 30 minutes at 120°C;
[0037] (3) Wash with hot water at 100°C for 5 minutes;
[0038] (4) Configure fresh working solution; containing 5g / L hydrophilic finishing agent KINDGER DF-C, 10g / L isopropanol;
[0039] (5) Place the fabric treated in step (3) in the fresh working solution prepared in step (4), and heat it up to 120°C for 20 minutes;
[0040] (6) Finally, wash with hot water above 90°C for 5-10 minutes.
[0041] The temperature of the step (3) is strictly controlled, and the repaired fabric can only be placed after t...
Embodiment 3
[0044] Cotton thick twill gauze garment fabric finished with Clariant chemical fluorine-free waterproofing agent FFR, specification: 16SX12S / 108X56, stripping fluorine-free waterproofing agent FFR, including the following specific steps:
[0045] (1) Configure the working solution; the working solution contains 10g / L silicon spot stripping agent FORYL CPH, 15g / L caustic soda;
[0046] (2) Put the fabric that needs to be repaired into the working fluid, and boil it for 45 minutes at 100°C;
[0047] (3) Wash with hot water at a temperature of 95°C for 10 minutes;
[0048] (4) Configure fresh working solution; containing 10g / L hydrophilic finishing agent KINDGER DF-C, 12g / L isopropanol;
[0049] (5) Place the fabric treated in step (3) in the fresh working solution prepared in step (4), and heat it up to 110°C for 25 minutes;
[0050] (6) Finally, wash with hot water above 90°C for 5-10 minutes.
[0051] The temperature of the step (3) is strictly controlled, and the repaired ...
PUM
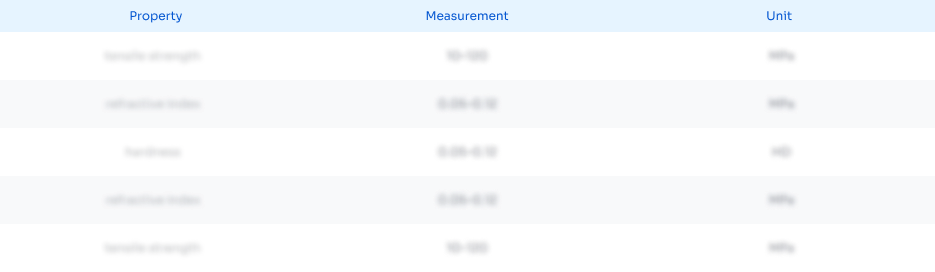
Abstract
Description
Claims
Application Information

- R&D
- Intellectual Property
- Life Sciences
- Materials
- Tech Scout
- Unparalleled Data Quality
- Higher Quality Content
- 60% Fewer Hallucinations
Browse by: Latest US Patents, China's latest patents, Technical Efficacy Thesaurus, Application Domain, Technology Topic, Popular Technical Reports.
© 2025 PatSnap. All rights reserved.Legal|Privacy policy|Modern Slavery Act Transparency Statement|Sitemap|About US| Contact US: help@patsnap.com