A kind of resistance wire alloy and its pre-oxidation treatment method
A technology of pre-oxidation treatment and resistance wire, applied in the direction of metal/alloy conductor, metal material coating process, etc., can solve the problem of short life of heating wire, achieve strong corrosion resistance, super insulation performance, and eliminate wrinkles. Effect
- Summary
- Abstract
- Description
- Claims
- Application Information
AI Technical Summary
Problems solved by technology
Method used
Examples
Embodiment 1
[0017] Implementation 1, take 24.9 kg of Cr, 5.35 kg of Al, 0.25 kg of Ti, 0.018 kg of C, 0.09 kg of Si, 0.0025 kg of S, 0.51 kg of Y, 0.18 kg of Mo, and 68.6995 kg of Fe.
[0018] The above alloy was smelted in an intermediate frequency vacuum induction furnace, and Y was added under argon protection three minutes before tapping. Dephosphorylation requires P <0.005%.
Embodiment 2
[0019] Implementation 2, take 20 kg of Cr, 5 kg of Al, 0.4 kg of Ti, 0.03 kg of C, 0.1 kg of Si, 0.003 kg of S, 0.6 kg of Y, 0.2 kg of Mo, and 73.667 kg of Fe.
[0020] The above alloy was smelted in an intermediate frequency vacuum induction furnace, and Y was added under argon protection three minutes before tapping. Dephosphorylation requires P <0.005%.
Embodiment 3
[0021] Implementation 3, take 26 kg of Cr, 3 kg of Al, 0.15 kg of Ti, 0.01 kg of C, 0.06 kg of Si, 0.003 kg of S, 0.4 kg of Y, 0.1 kg of Mo, and 70.227 kg of Fe.
[0022] The above alloy was smelted in an intermediate frequency vacuum induction furnace, and Y was added under argon protection three minutes before tapping. Dephosphorylation requires P <0.005%.
[0023] Process the obtained heating wire raw materials into wires, and then carry out pre-oxidation treatment,
[0024] (1) pickling
[0025] Use 8% (mass fraction) of ammonium citrate for the heating wire at 60°C for 40 minutes, wash it with cold water, then put it in an alkaline permanganate bath for 10 minutes, wash it with cold water for 2 minutes, and carry out pickling.
[0026] (2) passivation
[0027] For the electric heating wire after pickling, use the agent HNO3 40%+Na2Cr207H202 4% (mass fraction); temperature 50°C; time 18min; or temperature 28°C; time 30min,
[0028] (3) Pickling for descaling
[0029] ...
PUM
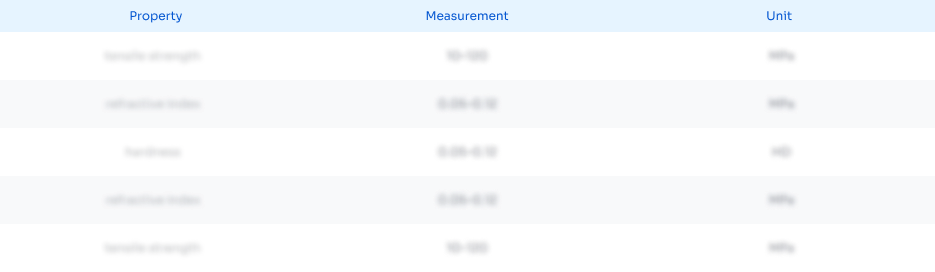
Abstract
Description
Claims
Application Information

- R&D Engineer
- R&D Manager
- IP Professional
- Industry Leading Data Capabilities
- Powerful AI technology
- Patent DNA Extraction
Browse by: Latest US Patents, China's latest patents, Technical Efficacy Thesaurus, Application Domain, Technology Topic, Popular Technical Reports.
© 2024 PatSnap. All rights reserved.Legal|Privacy policy|Modern Slavery Act Transparency Statement|Sitemap|About US| Contact US: help@patsnap.com