Manufacturing method of ultralow-voltage anodized aluminum foil
An anodizing, ultra-low voltage technology, applied in anodizing, electrolytic coating, surface reaction electrolytic coating, etc., can solve the problem of no report on the removal of natural oxide film, achieve the improvement of the specific volume of aluminum foil, increase the specific volume of aluminum foil Effect
- Summary
- Abstract
- Description
- Claims
- Application Information
AI Technical Summary
Problems solved by technology
Method used
Examples
Embodiment 1
[0020] 1) Chemical pretreatment: soak the corroded aluminum foil in an aqueous solution of oxalic acid with a mass concentration of 3% for treatment, and then thoroughly clean it with deionized water to obtain a pretreated aluminum foil; wherein, the treatment temperature is 7°C, and the treatment The time is 120s;
[0021] 2) Formation of aluminum foil: immerse the pretreated aluminum foil in an aqueous ammonium adipate solution with a mass concentration of 12% at 80°C, at a voltage of 4V and 50mA / cm 2 Carry out continuous anodizing under the current density until the anode aluminum foil is formed;
[0022] 3) Heat treatment: heat-treat the anode aluminum foil at 460°C for 2 minutes to obtain heat-treated aluminum foil;
[0023] 4) Compensation formation: the heat-treated aluminum foil is again anodized under the conditions of step 2) to perform supplementation formation;
[0024] 5) Hydration resistance treatment: Treat the formed aluminum foil at 60°C in an aqueous hypoph...
Embodiment 2
[0027] 1) Chemical pretreatment: soak the corroded aluminum foil in an acid solution with a mass concentration of 0.01% for treatment, and then fully clean it with deionized water to obtain a pretreated aluminum foil; wherein, the solute in the acid solution is made of Composition of acetic acid and lactic acid with a mass ratio of 1:1, the processing temperature is 90°C, and the processing time is 1s;
[0028] 2) Formation of aluminum foil: immerse the pretreated aluminum foil in an aqueous ammonium adipate solution with a mass concentration of 2% at 50°C, at a voltage of 13V and 5mA / cm 2 Carry out continuous anodizing under the current density until the anode aluminum foil is formed;
[0029] 3) Heat treatment: heat-treat the anode aluminum foil at 300°C for 5 minutes to obtain heat-treated aluminum foil;
[0030] 4) Compensation formation: the heat-treated aluminum foil is again anodized under the conditions of step 2) to perform supplementation formation;
[0031] 5) Hyd...
Embodiment 3
[0034] 1) Chemical pretreatment: soak the corroded aluminum foil in an aqueous sodium hydroxide solution with a mass concentration of 5% for treatment, and then fully clean it with deionized water to obtain a pretreated aluminum foil; wherein, the treatment temperature is 25°C , the processing time is 100s;
[0035] 2) Aluminum foil formation: immerse the pretreated aluminum foil in 90°C, 5% ammonium adipate aqueous solution at a voltage of 7V and 100mA / cm 2 Carry out continuous anodizing under the current density until the anode aluminum foil is formed;
[0036] 3) Heat treatment: heat-treat the anode aluminum foil at 600°C for 3 minutes to obtain heat-treated aluminum foil;
[0037] 4) Compensation formation: the heat-treated aluminum foil is again anodized under the conditions of step 2) to perform supplementation formation;
[0038] 5) Hydration-resistant treatment: Treat the formed aluminum foil at 80°C in a phosphorus-containing compound solution with a mass concentrat...
PUM
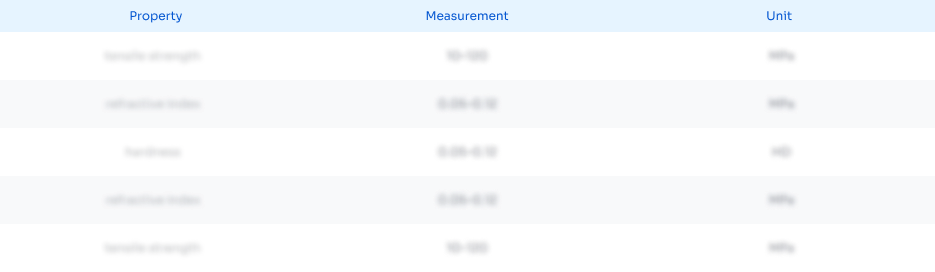
Abstract
Description
Claims
Application Information

- R&D
- Intellectual Property
- Life Sciences
- Materials
- Tech Scout
- Unparalleled Data Quality
- Higher Quality Content
- 60% Fewer Hallucinations
Browse by: Latest US Patents, China's latest patents, Technical Efficacy Thesaurus, Application Domain, Technology Topic, Popular Technical Reports.
© 2025 PatSnap. All rights reserved.Legal|Privacy policy|Modern Slavery Act Transparency Statement|Sitemap|About US| Contact US: help@patsnap.com