Preparation method of nano-fiber-foam-based acoustic material
A nanofiber and sound-absorbing material technology, applied in the direction of sound-producing equipment, instruments, etc., can solve the problems such as the inability to effectively achieve low-frequency noise absorption, limit the large-scale application of sound-absorbing materials, and poor sound-absorbing performance, and achieve great application prospects and commercial value. The effect of strong material structure design and excellent sound absorption performance
- Summary
- Abstract
- Description
- Claims
- Application Information
AI Technical Summary
Problems solved by technology
Method used
Examples
Embodiment 1
[0024] A preparation method of nanofiber foam-based sound-absorbing material, the specific steps are:
[0025] The first step: the surface of the nanofiber foam is activated by an alkali reduction method, wherein the alkali solution is a 2% sodium hydroxide solution by mass fraction, and the nanofiber foam is immersed in a 2% sodium hydroxide solution, and after 1 hour Take it out and wash it to neutral, then put it into a blast oven and dry it; the volume density of the nanofiber foam is 0.1mg / cm 3 , the average pore diameter is 0.01μm, and the specific surface area is 10m 2 / g; the nanofiber foam is a nanofiber foam with uniform overall density;
[0026] The second step: at a temperature of 32°C and a pressure of 7.39×10 6 Under the condition of Pa, the nanofiber foam obtained in the previous step was treated with a mixture of supercritical carbon dioxide fluid, adhesive agent and surface roughness modified particles, and then the pressure was reduced to 1.01×10 5 Pa, mak...
Embodiment 2
[0029] A preparation method of nanofiber foam-based sound-absorbing material, the specific steps are:
[0030]Step 1: Use solvent extraction method to activate the surface of nanofiber foam, wherein the extraction solvent is dichloromethane, the extraction time is 30min, and the number of extractions is 3 times, so that the surface soluble functional groups are removed by dichloromethane to form active sites point; the nanofiber foam bulk density is 50mg / cm 3 , the average pore diameter is 10μm, and the specific surface area is 2000m 2 / g; the nanofiber foam is a nanofiber foam material whose overall density changes uniformly along the thickness direction;
[0031] The second step: at a temperature of 35°C and a pressure of 7.4×10 6 Under the condition of Pa, the nanofiber foam obtained in the previous step was treated with a mixture of supercritical carbon dioxide fluid, adhesive agent and surface roughness modified particles, and then the pressure was reduced to 1.01×10 5...
Embodiment 3
[0034] A preparation method of nanofiber foam-based sound-absorbing material, the specific steps are:
[0035] Step 1: Activate the surface of the nanofiber foam by using the hydrothermal growth method, wherein the solution used in the hydrothermal growth method is a glucose solution with a mass fraction of 5%, the heating temperature is 200°C, the pressure is 10MPa, and the treatment time is 2 hours; The nanofiber foam bulk density is 5mg / cm 3 , the average pore diameter is 1μm, and the specific surface area is 1000m 2 / g; the nanofiber foam is a nanofiber foam material whose overall density changes gradiently along the thickness direction.
[0036] The second step: at a temperature of 34°C and a pressure of 7.5×10 6 Under the condition of Pa, the nanofiber foam obtained in the previous step was treated with a mixture of supercritical carbon dioxide fluid, adhesive agent and surface roughness modified particles, and then the pressure was reduced to 1.01×10 5 Pa, make the n...
PUM
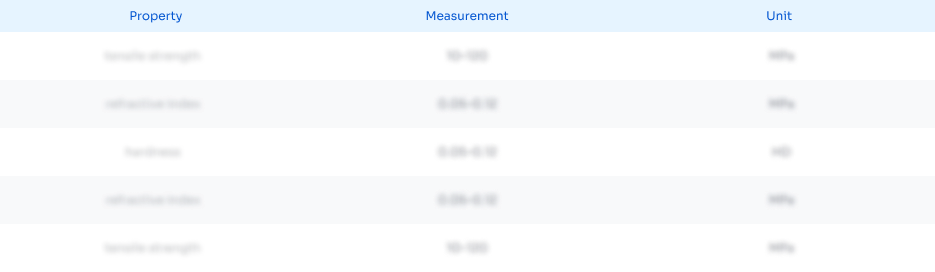
Abstract
Description
Claims
Application Information

- R&D
- Intellectual Property
- Life Sciences
- Materials
- Tech Scout
- Unparalleled Data Quality
- Higher Quality Content
- 60% Fewer Hallucinations
Browse by: Latest US Patents, China's latest patents, Technical Efficacy Thesaurus, Application Domain, Technology Topic, Popular Technical Reports.
© 2025 PatSnap. All rights reserved.Legal|Privacy policy|Modern Slavery Act Transparency Statement|Sitemap|About US| Contact US: help@patsnap.com