Oil-resistant rubber shoe sole
A technology of oil-resistant rubber and anti-aging agent, applied in the field of rubber soles, can solve the problems of needing plasticization, consuming manpower and material resources, increasing costs, etc., and achieving the effects of excellent oil resistance, saving manpower and energy consumption
- Summary
- Abstract
- Description
- Claims
- Application Information
AI Technical Summary
Problems solved by technology
Method used
Examples
Embodiment 1
[0011] A preparation method for oil-resistant rubber soles, comprising the following steps:
[0012] (1) Weigh by weight (kg):
[0013] NBR / PVC840,
[0015] Stearic acid 12,
[0016] Antiaging agent 12,
[0017] Coupling agent 18,
[0018] Dioctyl 110,
[0019] polyethylene glycol 8,
[0020] Sulfur 12,
[0021] Accelerator 14.
Embodiment 2
[0023] A preparation method for oil-resistant rubber soles, comprising the following steps:
[0024] (1) Weigh by weight (kg):
[0025] NBR / PVC960,
[0027] Stearic acid 24,
[0028] Antiaging agent 16,
[0029] Coupling agent 22,
[0030] Dioctyl 130,
[0031] polyethylene glycol 10,
[0032] sulfur 17,
[0033] Accelerator 30.
Embodiment 3
[0035] A preparation method for oil-resistant rubber soles, comprising the following steps:
[0036] (1) Weigh by weight (kg):
[0037] NBR / PVC900,
[0038] Magnesium oxide 45,
[0039] Stearic acid 18,
[0040] Antiaging agent 14,
[0041] Coupling agent 20,
[0042] Dioctyl 120,
[0043] polyethylene glycol 9,
[0044] Sulfur 15,
[0045] Accelerator 17.
PUM
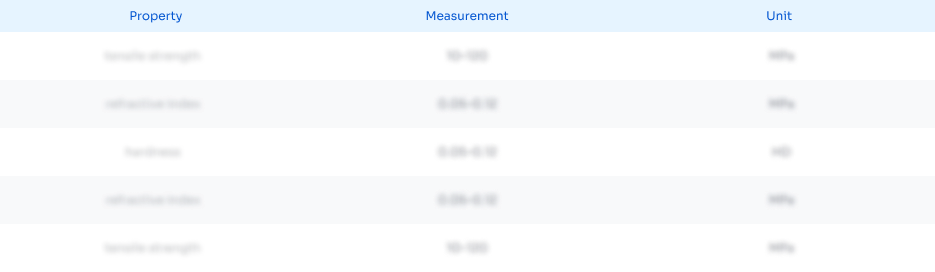
Abstract
Description
Claims
Application Information

- Generate Ideas
- Intellectual Property
- Life Sciences
- Materials
- Tech Scout
- Unparalleled Data Quality
- Higher Quality Content
- 60% Fewer Hallucinations
Browse by: Latest US Patents, China's latest patents, Technical Efficacy Thesaurus, Application Domain, Technology Topic, Popular Technical Reports.
© 2025 PatSnap. All rights reserved.Legal|Privacy policy|Modern Slavery Act Transparency Statement|Sitemap|About US| Contact US: help@patsnap.com