High-temperature-resistant ceramic material for manufacturing pot body
A technology of high temperature resistant ceramics and systems, applied in the field of high temperature resistant ceramic materials, can solve the problems of general heat resistance and other problems
- Summary
- Abstract
- Description
- Claims
- Application Information
AI Technical Summary
Problems solved by technology
Method used
Examples
Embodiment 1
[0015] This embodiment discloses a high-temperature-resistant ceramic material used in the manufacture of a pot body. The manufacturing method includes the following steps:
[0016] S1 Weigh raw materials according to the following parts by mass: 13 parts of purple sand, 7 parts of black soil, 16 parts of sericite, 6 parts of amphibole, 7 parts of vermiculite, 3 parts of pyroxene, 9 parts of granite, 8 parts of calcined talc, quartz 6 parts, mix the raw materials, put them into a ball mill and pass through a 250-mesh sieve, and set aside;
[0017] S2 dehydrating the product obtained in step S1;
[0018] S3 drying the dehydrated product in step S2, and calcining at a high temperature with heat preservation at a sintering temperature of 1320° C. and a heat preservation time of 30 minutes.
Embodiment 2
[0020] This embodiment discloses a high-temperature-resistant ceramic material used in the manufacture of a pot body. The manufacturing method includes the following steps:
[0021] S1 Weigh raw materials according to the following parts by mass: 11 parts of purple sand soil, 9 parts of black soil, 15 parts of sericite, 4 parts of amphibole, 9 parts of vermiculite, 2 parts of pyroxene, 11 parts of granite, 10 parts of calcined talc, quartz 4 parts, mix the raw materials, put them into a ball mill and pass through a 250-mesh sieve, and set aside;
[0022] S2 dehydrating the product obtained in step S1;
[0023] S3 drying the dehydrated product in step S2, and calcining at high temperature with heat preservation at a sintering temperature of 1380° C. and a heat preservation time of 30 minutes.
Embodiment 3
[0025] This embodiment discloses a high-temperature-resistant ceramic material used in the manufacture of a pot body. The manufacturing method includes the following steps:
[0026] S1 Weigh raw materials according to the following parts by mass: 18 parts of purple sand, 5 parts of black soil, 17 parts of sericite, 7 parts of amphibole, 3 parts of vermiculite, 4 parts of pyroxene, 8 parts of granite, 5 parts of calcined talc, quartz 7 parts, mix the raw materials, put them into a ball mill and pass through a 250-mesh sieve, and set aside;
[0027] S2 dehydrating the product obtained in step S1;
[0028] S3 drying the dehydrated product in step S2, and calcining at a high temperature with a sintering temperature of 1350° C. and a holding time of 30 minutes.
PUM
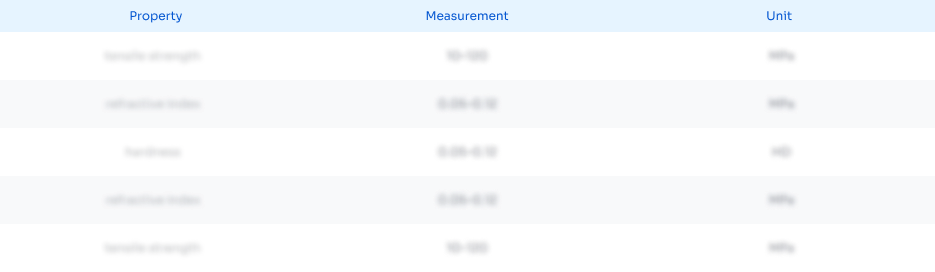
Abstract
Description
Claims
Application Information

- R&D Engineer
- R&D Manager
- IP Professional
- Industry Leading Data Capabilities
- Powerful AI technology
- Patent DNA Extraction
Browse by: Latest US Patents, China's latest patents, Technical Efficacy Thesaurus, Application Domain, Technology Topic, Popular Technical Reports.
© 2024 PatSnap. All rights reserved.Legal|Privacy policy|Modern Slavery Act Transparency Statement|Sitemap|About US| Contact US: help@patsnap.com