Method for forming ultra-thin stainless steel bend pipe
A stainless steel and elbow technology, applied in the field of ultra-thin stainless steel elbow forming, can solve problems such as low production efficiency, distortion of parts, out-of-tolerance roundness, etc., to improve forming accuracy, avoid wrinkling and section distortion, and improve products The effect of quality and reliability
- Summary
- Abstract
- Description
- Claims
- Application Information
AI Technical Summary
Problems solved by technology
Method used
Image
Examples
Embodiment Construction
[0016] In order to make the object and features of the present invention more obvious and understandable, below in conjunction with the attached figure 1 The specific embodiment of the present invention will be further described.
[0017] The present invention is achieved through the following scheme: the method comprises the following steps:
[0018] Step 1. Select the hollow stainless steel pipe fittings as the original blank. The wall thickness of the hollow pipe fittings is 0.8mm. There are two specifications of the pipe diameters, namely φ52mm and φ65mm. The hollow pipe fittings are seamless steel pipes. and other defects;
[0019] Step 2: insert the seamless steel pipe into the mandrel 7 of the forming mold, and adjust the process parameter mandrel extension to 20 mm, where the mandrel 7 protrusion refers to the length at which the mandrel is inserted into the beginning of bending. And apply lubricating oil evenly in the tube to prevent the core head 3 from scratching ...
PUM
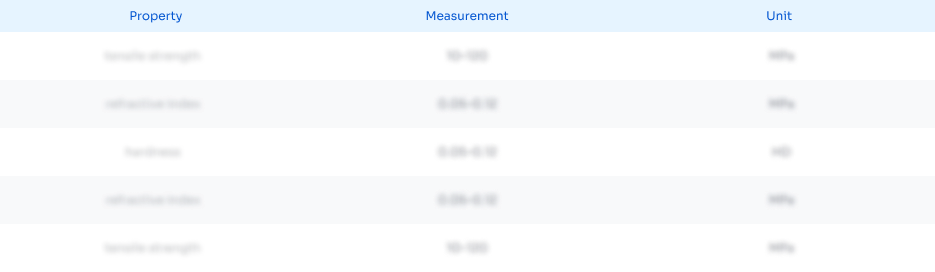
Abstract
Description
Claims
Application Information

- R&D
- Intellectual Property
- Life Sciences
- Materials
- Tech Scout
- Unparalleled Data Quality
- Higher Quality Content
- 60% Fewer Hallucinations
Browse by: Latest US Patents, China's latest patents, Technical Efficacy Thesaurus, Application Domain, Technology Topic, Popular Technical Reports.
© 2025 PatSnap. All rights reserved.Legal|Privacy policy|Modern Slavery Act Transparency Statement|Sitemap|About US| Contact US: help@patsnap.com