Cold rolling method capable of preventing edge crack and brittle fracture of silicon steel with Si content more than or equal to 3.5 percent
A technology of edge cracking and brittle fracture, applied in metal rolling, temperature control, etc., can solve the problems of difficult precise control of plate shape, burning of roll surface, uneven lateral distribution of temperature, etc., to improve the yield of finished products and improve the magnetic properties Effect
- Summary
- Abstract
- Description
- Claims
- Application Information
AI Technical Summary
Problems solved by technology
Method used
Examples
Embodiment 1
[0023] The Si of the present embodiment is the silicon steel of 3.52%, and its cold rolling step:
[0024] 1) Preheat the uncoiled steel plate first, and the preheating temperature is 63°C;
[0025] 2) Emulsion is used for spraying, the flow rate of the emulsion on the inlet side is 1000L / min, and the flow rate of the emulsion on the outlet side of the first 1 to 4 passes is completely closed;
[0026] 3) Cold rolling is carried out by one-time cold rolling method, during which: the reduction rate of the first pass is 36%, the reduction rate of the last pass is 25%, and the reduction rate of the remaining passes is in the range of 25%~34% Inside; the rolling deformation temperature of the first pass is 115°C, the rolling deformation temperature of the 2nd to 4th passes is 190°C, and the rolling deformation temperature of the remaining passes is 82°C;
[0027] 4) Perform coiling, where the tension at the set coiling speed is 20kg / mm 2 , from the beginning of coiling to the in...
Embodiment 2
[0031] The Si of the present embodiment is the silicon steel of 3.52%, and its cold rolling step:
[0032] 1) Preheat the uncoiled steel plate first, and the preheating temperature is 78°C;
[0033] 2) Emulsion is used for spraying, the flow rate of the emulsion on the inlet side is 2000L / min, and the flow rate of the emulsion on the outlet side of the first 1 to 4 passes is completely closed;
[0034] 3) Cold rolling is carried out by one-time cold rolling method, during which: the reduction rate of the first pass is 38%, the reduction rate of the last pass is 27%, and the reduction rate of the remaining passes is in the range of 25%~31% Inside; the rolling deformation temperature of the first pass is 132°C, the rolling deformation temperature of the 2nd to 4th passes is 200°C, and the rolling deformation temperature of the remaining passes is 85°C;
[0035] 4) Perform coiling, wherein the tension at the set coiling speed is 16kg / mm 2 , from the beginning of coiling to the ...
Embodiment 3
[0039] The Si of the present embodiment is the silicon steel of 3.51%, and its cold rolling step:
[0040] 1) Preheat the uncoiled steel plate first, and the preheating temperature is 72°C;
[0041] 2) Use emulsion for spraying, the flow rate of the emulsion on the inlet side is 3000L / min, and the flow rate of the emulsion on the outlet side of the first 1 to 4 passes is completely closed;
[0042] 3) Cold rolling is carried out by one-time cold rolling method, during which: the reduction rate of the first pass is 41%, the reduction rate of the last pass is 21%, and the reduction rate of the remaining passes is in the range of 28%~30% Inside; the rolling deformation temperature of the first pass is 142°C, the rolling deformation temperature of the 1st to 4th passes is 212°C, and the rolling deformation temperature of the remaining passes is 75°C;
[0043] 4) Perform coiling, where the tension at the set coiling speed is 22kg / mm 2 , from the beginning of coiling to the initia...
PUM
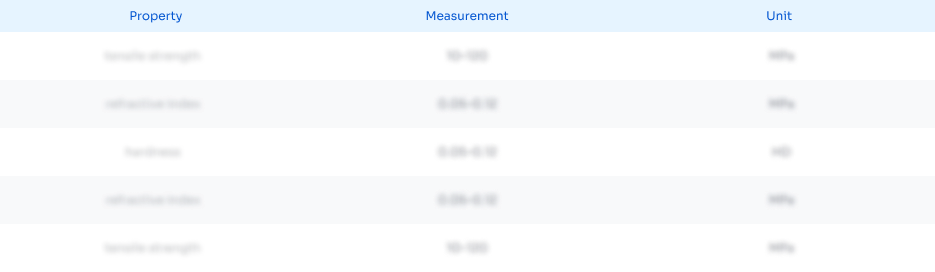
Abstract
Description
Claims
Application Information

- Generate Ideas
- Intellectual Property
- Life Sciences
- Materials
- Tech Scout
- Unparalleled Data Quality
- Higher Quality Content
- 60% Fewer Hallucinations
Browse by: Latest US Patents, China's latest patents, Technical Efficacy Thesaurus, Application Domain, Technology Topic, Popular Technical Reports.
© 2025 PatSnap. All rights reserved.Legal|Privacy policy|Modern Slavery Act Transparency Statement|Sitemap|About US| Contact US: help@patsnap.com