Machining process for strain-hardening seal head
A technology of strain strengthening and processing technology, which is applied in the direction of pressure vessels, fixed-capacity gas storage tanks, mechanical equipment, etc., can solve problems such as the drop, the inner surface finish of the head is not enough, the appearance quality of the head can not meet the requirements of use, etc., to achieve Ensure uniformity and avoid the effect of coarse weld grains
- Summary
- Abstract
- Description
- Claims
- Application Information
AI Technical Summary
Problems solved by technology
Method used
Examples
Embodiment Construction
[0017] The present invention will now be described in further detail in conjunction with embodiments.
[0018] A processing technology for strain-strengthened heads specifically includes the following steps:
[0019] 1) Pre-qualify the welding process for the welded joints, in which a set of conventional assessments and a set of samples after 9% tensile deformation are required to determine the tensile strength and other performance parameters of the welded joints.
[0020] 2) Select austenitic stainless steel sheet with appropriate post-tensile strength according to the evaluated performance, cut the steel plate according to the size required by the process with a plasma cutting machine, and cut and polish the welding groove according to the process card requirements, and perform the end of the wafer Chamfering and grinding treatment;
[0021] 3) Tailor-welded wafers are made by welding two crescent-shaped plates. Plasma welding with concentrated heat and automatic argon tungsten arc...
PUM
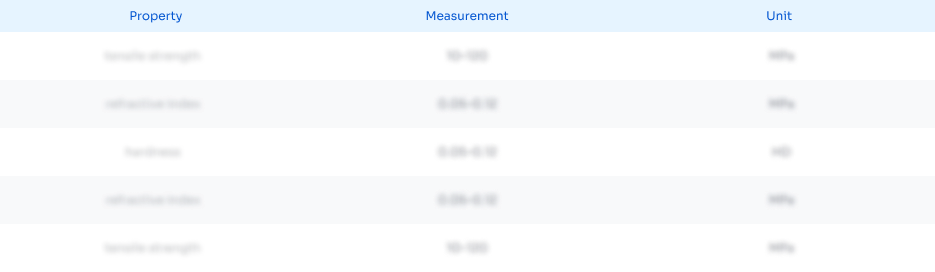
Abstract
Description
Claims
Application Information

- R&D
- Intellectual Property
- Life Sciences
- Materials
- Tech Scout
- Unparalleled Data Quality
- Higher Quality Content
- 60% Fewer Hallucinations
Browse by: Latest US Patents, China's latest patents, Technical Efficacy Thesaurus, Application Domain, Technology Topic, Popular Technical Reports.
© 2025 PatSnap. All rights reserved.Legal|Privacy policy|Modern Slavery Act Transparency Statement|Sitemap|About US| Contact US: help@patsnap.com