Ultra -high -stick precision cotton production process
A production process and refined cotton technology, applied in pulping with inorganic alkali, pretreatment of finely split raw materials, textiles and papermaking, etc., can solve the problems of affecting product viscosity, simple cooking process, unfavorable cooking treatment, etc., and achieve improvement The effect of product viscosity, reducing the cost of use, and meeting the whiteness requirements
- Summary
- Abstract
- Description
- Claims
- Application Information
AI Technical Summary
Problems solved by technology
Method used
Examples
Embodiment 1
[0007] Embodiment 1: ultra-high-viscosity refined cotton production process, its specific production process is as follows: a, material selection, cotton opening: select 4 tons of high-quality cotton linters without three silk impurities as raw material, and the fiber length of cotton linters is between 13 ~ 15mm, absolute dryness is 92%, maturity is over 80%, and has been treated with loosening, impurity removal and cotton opening; The final cotton linters are sprayed with a dissolving ratio of 1:2.7. After extrusion treatment at 0.18MPa, the sodium hydroxide solution is fully and evenly penetrated into the cotton linters to form alkali fibers, and the humidity of the alkali fibers is controlled at 78%; c , Pretreatment: The alkali fibers after soaking in alkali fully and uniformly are subjected to 2MPa rolling treatment, and the lye solution rolled out is recycled and reused. After rolling, the humidity of the alkali fibers is controlled at 45%, and then the mass concentratio...
Embodiment 2
[0008] Embodiment 2: ultra-high-viscosity refined cotton production process, its specific production process is as follows: a, material selection, cotton opening: select 4 tons of high-quality cotton linters without three silk impurities as raw material, and the fiber length of cotton linters is between 13 ~ 15mm, absolute dryness is 92%, maturity is over 80%, and has been treated with loosening, impurity removal and cotton opening; The final cotton linters are sprayed with a solvent ratio of 1:3.0, and after extrusion treatment at 0.20 MPa, the sodium hydroxide solution is fully and evenly penetrated into the cotton linters to form alkali fibers, and the humidity of the alkali fibers is controlled at 75%; c , pretreatment: the alkali fiber after soaking in alkali fully and evenly is processed through 3MPa rolling, and the lye liquid that is rolled out is recycled and reused. 4 kg of AES auxiliary agent is used to perform three times of repeated spraying and rolling treatment ...
Embodiment 3
[0009]Embodiment 3: ultra-high-viscosity refined cotton production process, its specific production process is as follows: a, material selection, cotton opening: select 4 tons of high-quality cotton linters without three silk impurities as raw material, and the fiber length of cotton linters is between 13 ~ 15mm, absolute dryness is 92%, maturity is over 80%, and has been treated with loosening, impurity removal and cotton opening; The final cotton linters are sprayed with a solvent ratio of 1:2.8, and after extrusion treatment at 0.19MPa, the sodium hydroxide solution is fully and evenly penetrated into the cotton linters to form alkali fibers, and the humidity of the alkali fibers is controlled at 76%; c , Pretreatment: The alkali fibers after soaking in alkali fully and evenly are subjected to 2.8MPa rolling treatment, and the lye solution rolled out is recycled and reused. After rolling, the humidity of the alkali fibers is controlled between 43%, and then the mass concentr...
PUM
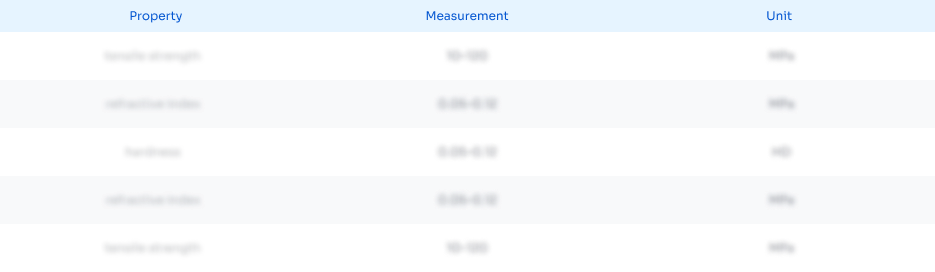
Abstract
Description
Claims
Application Information

- R&D Engineer
- R&D Manager
- IP Professional
- Industry Leading Data Capabilities
- Powerful AI technology
- Patent DNA Extraction
Browse by: Latest US Patents, China's latest patents, Technical Efficacy Thesaurus, Application Domain, Technology Topic, Popular Technical Reports.
© 2024 PatSnap. All rights reserved.Legal|Privacy policy|Modern Slavery Act Transparency Statement|Sitemap|About US| Contact US: help@patsnap.com