Netted structure frame and manufacturing method thereof
A technique of mesh structure and manufacturing method, applied in bicycle racks, bicycle accessories, transportation and packaging, etc., can solve the problems of poor rigidity/weight, increased riding resistance, and no advantages of weight/rigidity
- Summary
- Abstract
- Description
- Claims
- Application Information
AI Technical Summary
Problems solved by technology
Method used
Image
Examples
Embodiment Construction
[0021] The present invention will be further described below in conjunction with the accompanying drawings and specific embodiments.
[0022] Such as figure 1 , figure 2 As shown, a frame with a mesh structure includes a frame body 1, and the frame body 1 includes a seat tube 101, an upper tube 102, a head tube 103, a lower tube 104, etc., which is different from the conventional carbon fiber frame in the prior art (See image 3 ) and ordinary grid-like rib structure frame (see Figure 4 ), the inventive point of the present invention is that the cross section of the vehicle frame body 1 is followed by the carbon fiber inner auxiliary layer 11, the carbon fiber mesh rib structure 12, and the carbon fiber outer auxiliary layer 13 from the inside to the outside. The carbon fiber inner auxiliary layer 11, The carbon fiber grid rib structure 12 and the carbon fiber outer auxiliary layer 13 are tightly combined. At the same time, the number of ribs in the carbon fiber grid rib...
PUM
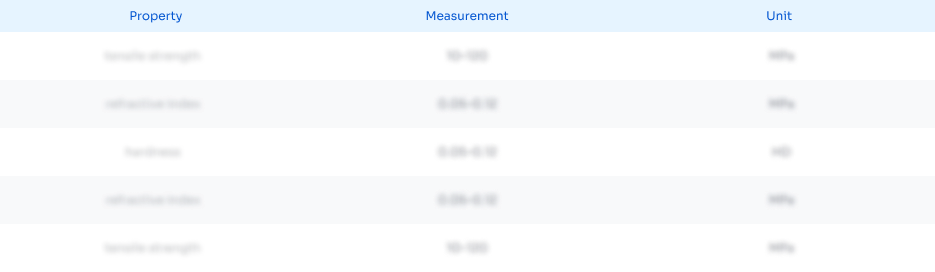
Abstract
Description
Claims
Application Information

- R&D Engineer
- R&D Manager
- IP Professional
- Industry Leading Data Capabilities
- Powerful AI technology
- Patent DNA Extraction
Browse by: Latest US Patents, China's latest patents, Technical Efficacy Thesaurus, Application Domain, Technology Topic, Popular Technical Reports.
© 2024 PatSnap. All rights reserved.Legal|Privacy policy|Modern Slavery Act Transparency Statement|Sitemap|About US| Contact US: help@patsnap.com