Process for manufacturing straight-bar stator cores
A straight-strip stator and manufacturing process technology, which is applied to the manufacturing process field of straight-strip stator iron cores, can solve the problems of high defective rate of welded and formed stator iron cores, increase process and processing costs, affect magnetic flux, etc., and reduce the number of processes. , The effect of improving welding yield and reducing cost
- Summary
- Abstract
- Description
- Claims
- Application Information
AI Technical Summary
Problems solved by technology
Method used
Image
Examples
Embodiment Construction
[0020] The present invention will be further described below in conjunction with accompanying drawing.
[0021] Such as figure 2 As shown, the straight stator sheet formed after the strip is punched, in this embodiment, the welding grooves used in the mold are 2, 31, 51, 80, and the welding grooves outside the mold are 11, 21, 41, 61, 71 .
[0022] Such as image 3 As shown, according to the process flow diagram, the manufacturing process of the straight stator core includes a strip and a progressive stamping die for stamping the strip. It is characterized in that it includes the following steps:
[0023] ① Stamping forming: Unroll and flatten the strip material and send it to the punching machine, and use the progressive stamping die to stamp out the straight stator single-piece groove, welding groove and shape; in the stamping procedure described above, set N pieces per stamping The size of the welding slot of the next N+1 piece is larger than that of a conventional ...
PUM
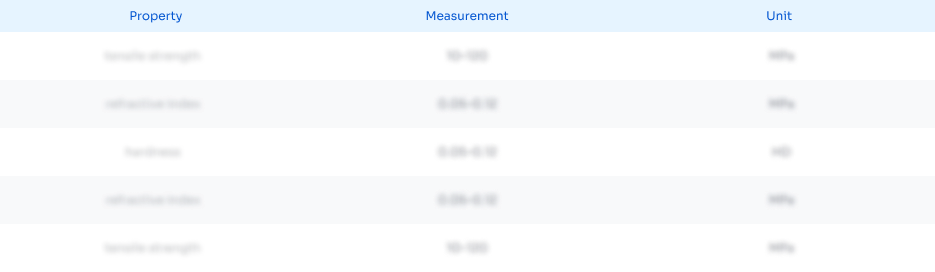
Abstract
Description
Claims
Application Information

- Generate Ideas
- Intellectual Property
- Life Sciences
- Materials
- Tech Scout
- Unparalleled Data Quality
- Higher Quality Content
- 60% Fewer Hallucinations
Browse by: Latest US Patents, China's latest patents, Technical Efficacy Thesaurus, Application Domain, Technology Topic, Popular Technical Reports.
© 2025 PatSnap. All rights reserved.Legal|Privacy policy|Modern Slavery Act Transparency Statement|Sitemap|About US| Contact US: help@patsnap.com