Torque transmission joint and electric power steering device
A torque transmission and axial technology, applied in the transmission device, gear transmission device, power steering mechanism, etc., can solve the problems of reduced operating efficiency, increased frictional resistance, and reduced transmission efficiency, so as to improve operating efficiency, reduce costs, and improve The effect of recognition
- Summary
- Abstract
- Description
- Claims
- Application Information
AI Technical Summary
Problems solved by technology
Method used
Image
Examples
Embodiment Construction
[0093] The first example of embodiment
[0094] Figure 1 to Figure 16 The first example of the embodiment of the present invention is shown. The electric power steering device of this example basically also includes: a casing 3, which is supported on a fixed part of the vehicle (the vehicle body or a part fixed to the vehicle body), and does not rotate; Freely arranged in the housing 3, the steering shaft 2 is rotated by the operation of the steering wheel 1, and the steering shaft 2 applies a steering angle to the steering wheel as it rotates; the worm 5 includes a worm wheel 4, a worm shaft 6a and a worm tooth 7, The worm wheel 4 is supported on a part of the steering shaft 2 concentrically with the steering shaft 2 inside the casing 3, and the worm wheel 4 rotates together with the steering shaft 2. The worm gear 7 is provided at the axially intermediate portion of the worm shaft 6a, and is used to In the state where the worm gear 7 is meshed with the worm wheel 4, the a...
PUM
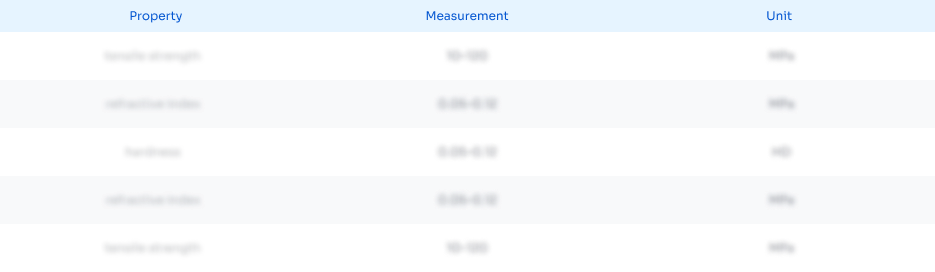
Abstract
Description
Claims
Application Information

- R&D
- Intellectual Property
- Life Sciences
- Materials
- Tech Scout
- Unparalleled Data Quality
- Higher Quality Content
- 60% Fewer Hallucinations
Browse by: Latest US Patents, China's latest patents, Technical Efficacy Thesaurus, Application Domain, Technology Topic, Popular Technical Reports.
© 2025 PatSnap. All rights reserved.Legal|Privacy policy|Modern Slavery Act Transparency Statement|Sitemap|About US| Contact US: help@patsnap.com