Making method of heavy gauge composite material main beam cap for fan blades
A composite material, fan blade technology, applied in the direction of final product manufacturing, sustainable manufacturing/processing, application, etc., can solve the process efficiency and process quality effect is difficult to guarantee, low process efficiency, can not adapt to the main spar cap process efficiency and process Quality requirements and other issues, to achieve the effect of solving the problems of preparation process efficiency and process quality, and reducing process control
- Summary
- Abstract
- Description
- Claims
- Application Information
AI Technical Summary
Problems solved by technology
Method used
Image
Examples
Embodiment 1
[0020] A large-scale carbon fiber / glass fiber uniaxially stitched braided fabric reinforced resin-based composite spar cap, the steps are as follows:
[0021] (1) if figure 1 Shown is a schematic diagram of the process layout of the main spar cap manufacturing process method of the present invention. First, the surface of the main spar cap forming mold 1 is cleaned, coated with a release agent, and then the first layer of release cloth 3 is laid sequentially, and the bottom guide The mesh 4 and the second layer of release cloth 5 and other process auxiliary materials are then cut and placed on the second layer of release cloth 5 according to the design specifications, size and number of layers to prepare the carbon fiber / glass fiber uniaxial for the main spar cap. Stitch-bonded fabric reinforcing material 2, and then on the carbon fiber / glass fiber uniaxial stitch-bonded fabric reinforcing material 2, process auxiliary materials such as the third layer of release cloth 6 and t...
PUM
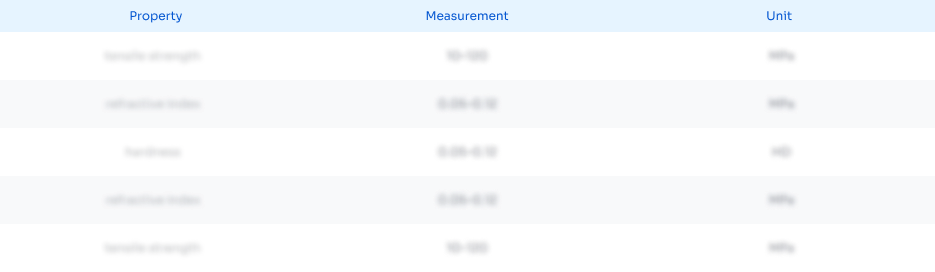
Abstract
Description
Claims
Application Information

- R&D
- Intellectual Property
- Life Sciences
- Materials
- Tech Scout
- Unparalleled Data Quality
- Higher Quality Content
- 60% Fewer Hallucinations
Browse by: Latest US Patents, China's latest patents, Technical Efficacy Thesaurus, Application Domain, Technology Topic, Popular Technical Reports.
© 2025 PatSnap. All rights reserved.Legal|Privacy policy|Modern Slavery Act Transparency Statement|Sitemap|About US| Contact US: help@patsnap.com