Preparation method of composite polytetrafluoroethylene nano-filtration membrane
A polytetrafluoroethylene and composite nanofiltration membrane technology, which is applied in chemical instruments and methods, membrane technology, semi-permeable membrane separation, etc., can solve the problems of complex structure and complex preparation process of nanofiltration membranes
- Summary
- Abstract
- Description
- Claims
- Application Information
AI Technical Summary
Problems solved by technology
Method used
Image
Examples
Embodiment 1
[0027] (1) Activation: Submerge the hydrophobic polytetrafluoroethylene flat membrane in a 0.1% mass concentration of sodium dodecylbenzenesulfonate aqueous solution for 12 hours; take it out and dry it in the air to obtain an active base membrane;
[0028] (2) Water phase impregnation: immerse the active base film described in step (1) in an aqueous solution of 0.1% piperazine by mass concentration, stay for 30 minutes, take it out and dry it in the air to obtain the intermediate film 1;
[0029] (3) Oil phase impregnation: immerse the intermediate film 1 described in step (2) in the n-hexane solution of trimesoyl chloride with a mass concentration of 0.1%, stay for 30 minutes, and then place it in the air to dry to obtain the intermediate film 2 ;
[0030] (4) Water phase impregnation: immerse the intermediate membrane 2 described in step (3) in an aqueous solution of piperazine with a mass concentration of 3.0%, stay for 10 minutes, take it out and dry it to obtain the inte...
Embodiment 2
[0035] (1) Activation: Submerge the hydrophobic polytetrafluoroethylene flat film in a 4.0% mass concentration of sodium dodecylbenzenesulfonate aqueous solution for 5 minutes; take it out and dry it in the air to obtain an active base film;
[0036] (2) Water phase impregnation: immerse the active base film described in step (1) in an aqueous solution of 5.0% by mass concentration of p-phenylenediamine, stay for 5 seconds, take it out and dry it in the air to obtain the intermediate film 1;
[0037] (3) Oil phase impregnation: immerse the intermediate film 1 described in step (2) in a toluene solution of 5.0% mass concentration of isophthaloyl chloride, stay for 5 seconds, and then place it in the air to dry to obtain the intermediate film 2 ;
[0038](4) Water-phase impregnation: immerse the intermediate film 2 described in step (3) in an aqueous solution of 0.1% p-phenylenediamine in mass concentration, stay for 30 minutes, take it out and dry it to obtain the intermediate ...
Embodiment 3
[0043] (1) Activation: Submerge the hydrophobic polytetrafluoroethylene flat membrane in a 2.0% mass concentration of sodium dodecylbenzenesulfonate aqueous solution for 1 hour; take it out and dry it in the air to obtain an active base membrane;
[0044] (2) Water phase impregnation: immerse the active base film described in step (1) in an aqueous solution of ethylenediamine with a mass concentration of 3.0%, stay for 10 minutes, take it out and dry it in the air to obtain the intermediate film 1;
[0045] (3) Oil phase impregnation: immerse the intermediate film 1 described in step (2) in a n-heptane solution of 3.0% by mass concentration of terephthaloyl chloride, stay for 10 minutes, and then place it in the air to dry to obtain an intermediate membrane2;
[0046] (4) Water phase immersion: immerse the intermediate membrane 2 described in step (3) in an aqueous solution of 5.0% mass concentration of ethylenediamine, stay for 5 seconds, take it out and dry it to obtain the ...
PUM
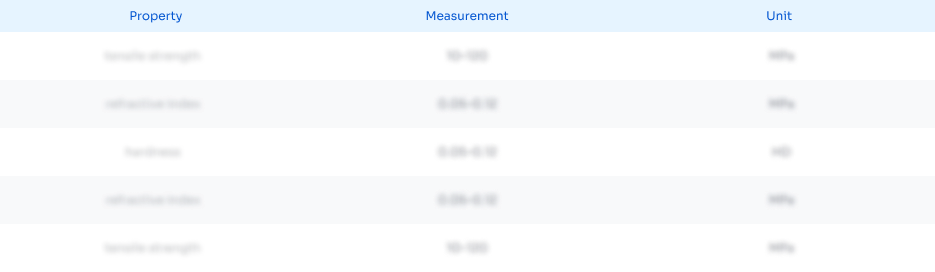
Abstract
Description
Claims
Application Information

- R&D Engineer
- R&D Manager
- IP Professional
- Industry Leading Data Capabilities
- Powerful AI technology
- Patent DNA Extraction
Browse by: Latest US Patents, China's latest patents, Technical Efficacy Thesaurus, Application Domain, Technology Topic, Popular Technical Reports.
© 2024 PatSnap. All rights reserved.Legal|Privacy policy|Modern Slavery Act Transparency Statement|Sitemap|About US| Contact US: help@patsnap.com