Threaded rod for polymer microcellular foaming injection molding
A technology of microcellular foaming and injection molding, which is applied in the injection molding machine system and the screw field of polymer microcellular foaming injection molding, can solve the problem of affecting the mixing ability and versatility of the screw, increasing the processing difficulty and precision, and having no intermediate stoppage. Inverse function and other problems, to achieve the effect of easy guarantee of processing accuracy, rapid and uniform distribution and dissolution, and guarantee of melt conveying efficiency
- Summary
- Abstract
- Description
- Claims
- Application Information
AI Technical Summary
Problems solved by technology
Method used
Image
Examples
Embodiment Construction
[0027] The present invention will be further described below in conjunction with the accompanying drawings and embodiments.
[0028] like Figure 1-3 As shown, a screw for polymer microcellular foaming injection molding, including screw polished rod part 1, screw feeding section 2, screw compression section 3, screw metering section 4, middle check ring 5, shearing section 6, mixing Section 7, front check ring 8, screw head 9.
[0029] Among them, the tail of the polished rod part 1 of the screw is provided with a keyway, and the screw is installed on the injection molding machine through the keyway and the key; The length is 1D (D is the diameter of the screw, D=60mm); in front of the screw metering section 4 is the middle non-return ring 5, the middle non-return ring 5 adopts the half-ring form with two steps disconnected, and is set on the stepped shaft of the screw. Considering the strength, processing difficulty and precision of the screw, the stepped shaft is integrall...
PUM
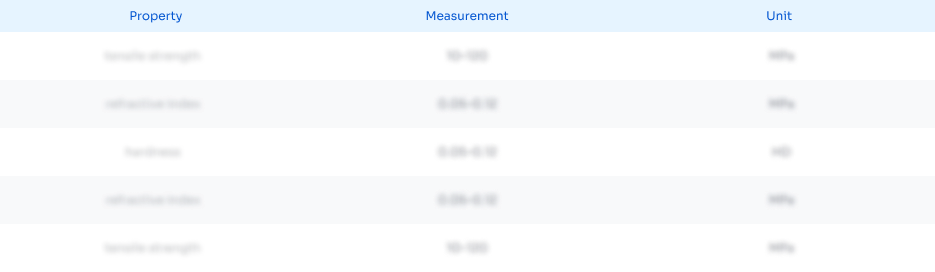
Abstract
Description
Claims
Application Information

- R&D
- Intellectual Property
- Life Sciences
- Materials
- Tech Scout
- Unparalleled Data Quality
- Higher Quality Content
- 60% Fewer Hallucinations
Browse by: Latest US Patents, China's latest patents, Technical Efficacy Thesaurus, Application Domain, Technology Topic, Popular Technical Reports.
© 2025 PatSnap. All rights reserved.Legal|Privacy policy|Modern Slavery Act Transparency Statement|Sitemap|About US| Contact US: help@patsnap.com