Aerated concrete block production system
A technology of aerated concrete and production system, applied in ceramic molding workshops, auxiliary molding equipment, ceramic molding machines, etc., can solve the problems of shortening the service life of feeding devices, increasing costs, waste of raw materials, etc., to improve production efficiency, avoid Winding, cost reduction effect
- Summary
- Abstract
- Description
- Claims
- Application Information
AI Technical Summary
Problems solved by technology
Method used
Image
Examples
Embodiment Construction
[0062] The present invention will be further described below in conjunction with the embodiments and accompanying drawings.
[0063] Such as Figure 1 to Figure 17 As shown, a production system for aerated concrete blocks includes a batching tank 1, an aerated concrete block cutting machine 2 and an autoclave 3, wherein a material is arranged between the batching tank 1 and the aerated concrete block cutting machine 2 A slurry forming transfer mechanism, a block transport mechanism 4 is provided between the aerated concrete block cutting machine 2 and the autoclave 3, and the top of the batching tank 1 communicates with the lime storage tank 5 and the cement storage tank 6 respectively , a grouting pool a is provided directly below the batching tank 1, a cutting pool b is provided directly below the aerated concrete block cutting machine 2, and between the grouting pool a and the cutting pool b A recovery pool c is provided, the grouting pool a and the cutting pool b communic...
PUM
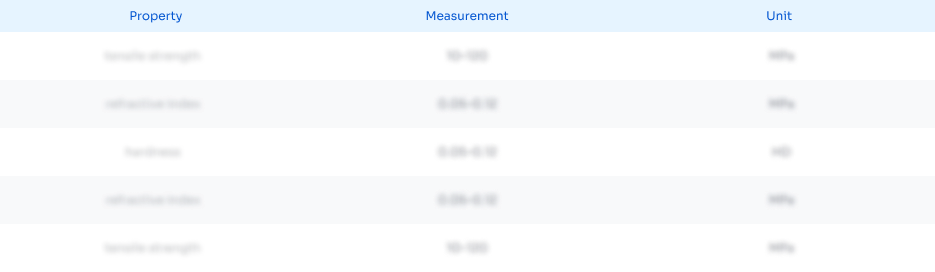
Abstract
Description
Claims
Application Information

- R&D
- Intellectual Property
- Life Sciences
- Materials
- Tech Scout
- Unparalleled Data Quality
- Higher Quality Content
- 60% Fewer Hallucinations
Browse by: Latest US Patents, China's latest patents, Technical Efficacy Thesaurus, Application Domain, Technology Topic, Popular Technical Reports.
© 2025 PatSnap. All rights reserved.Legal|Privacy policy|Modern Slavery Act Transparency Statement|Sitemap|About US| Contact US: help@patsnap.com