Veneer pretreatment device
A pretreatment device, veneer technology, used in grinding/polishing safety devices, grinding machines, machine tools suitable for grinding workpiece planes, etc. problem, to achieve the effect of protecting the veneer surface
- Summary
- Abstract
- Description
- Claims
- Application Information
AI Technical Summary
Problems solved by technology
Method used
Image
Examples
Embodiment 1
[0037] This embodiment includes veneer conveying roller 1, primary grinding roller 2 and impurity removal mechanism. There are three primary grinding rollers 2, namely primary primary grinding roller 3, secondary primary grinding roller 4 and tertiary primary grinding roller 5, The installation height of the first primary grinding roller 3 is lower than that of the secondary primary grinding roller 4, and the installation height of the secondary primary grinding roller 4 and the third primary grinding roller 5 is the same. Primary grinding roller, secondary primary grinding roller, tertiary primary grinding roller and impurity removal mechanism. The first-level initial grinding roller 3, the second-level initial grinding roller 4 and the third-level initial grinding roller 5 are all provided with grinding protrusions, and the grinding protrusions on the first-level initial grinding roller are higher than the height of the first-level initial grinding roller. The grinding protr...
Embodiment 2
[0039] This embodiment includes veneer conveying roller 1, primary grinding roller 2 and impurity removal mechanism. There are three primary grinding rollers 2, namely primary primary grinding roller 3, secondary primary grinding roller 4 and tertiary primary grinding roller 5, The installation height of the first primary grinding roller 3 is lower than that of the secondary primary grinding roller 4, and the installation height of the secondary primary grinding roller 4 and the third primary grinding roller 5 is the same. Primary grinding roller, secondary primary grinding roller, tertiary primary grinding roller and impurity removal mechanism. A deviation correction roller 6 is also arranged between the impurity removal mechanism and the third primary grinding roller 5 , and the installation height of the deviation correction roller 6 is lower than that of the third primary grinding roller 5 . The first-level initial grinding roller 3, the second-level initial grinding rolle...
Embodiment 3
[0041] This embodiment includes veneer conveying roller 1, primary grinding roller 2 and impurity removal mechanism. There are three primary grinding rollers 2, namely primary primary grinding roller 3, secondary primary grinding roller 4 and tertiary primary grinding roller 5, The installation height of the first primary grinding roller 3 is lower than that of the secondary primary grinding roller 4, and the installation height of the secondary primary grinding roller 4 and the third primary grinding roller 5 is the same. Primary grinding roller, secondary primary grinding roller, tertiary primary grinding roller and impurity removal mechanism. A deviation correction roller 6 is also arranged between the impurity removal mechanism and the third primary grinding roller 5 , and the installation height of the deviation correction roller 6 is lower than that of the third primary grinding roller 5 . The impurity removal mechanism comprises an impurity removal platform 7, an impuri...
PUM
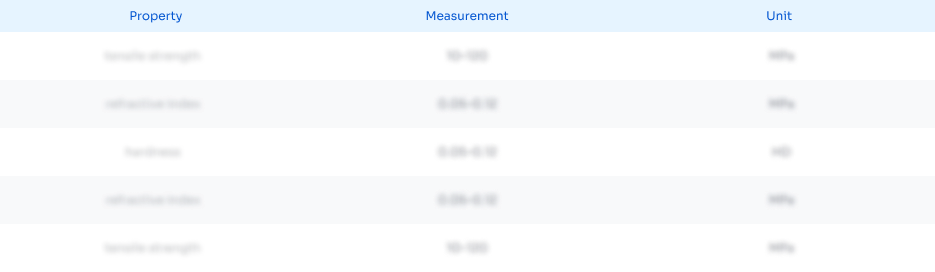
Abstract
Description
Claims
Application Information

- R&D
- Intellectual Property
- Life Sciences
- Materials
- Tech Scout
- Unparalleled Data Quality
- Higher Quality Content
- 60% Fewer Hallucinations
Browse by: Latest US Patents, China's latest patents, Technical Efficacy Thesaurus, Application Domain, Technology Topic, Popular Technical Reports.
© 2025 PatSnap. All rights reserved.Legal|Privacy policy|Modern Slavery Act Transparency Statement|Sitemap|About US| Contact US: help@patsnap.com