GPP rectification chip based on reverse grooving technology
A technology of rectifying chips and reverse digging, which is applied in the direction of electrical components, electrical solid devices, circuits, etc., and can solve problems such as assembly difficulties, flashover, and two-electrode short circuits for subsequent customers
- Summary
- Abstract
- Description
- Claims
- Application Information
AI Technical Summary
Problems solved by technology
Method used
Image
Examples
Embodiment Construction
[0020] Mainly explain the formula and steps used in the implementation of the P-type impurity diffusion process in the process of producing GPP rectifier chips based on the back-grooving process:
[0021] The P-type diffusion impurity source formula is boric acid: aluminum nitrate: dehydrated alcohol, and the weight ratio is 9: 20: 80;
[0022] On the surface of the single crystal silicon wafer without phosphorus deposition, spin-coat the P-type diffusion impurity source, the equivalent coating amount is to coat 0.16 ml of phosphorus source solution on each side of each 3-inch single crystal silicon wafer, and the spin coating speed is 30 rpm Strictly control the reverse osmosis of the P-type diffusion impurity source to the phosphorus deposition surface. If there is a small amount of seepage on the edge of the phosphorus deposition surface, wipe it with a chemical fiber cloth dipped in absolute ethanol. The coated monocrystalline silicon wafer can be heated Plate or infrared ...
PUM
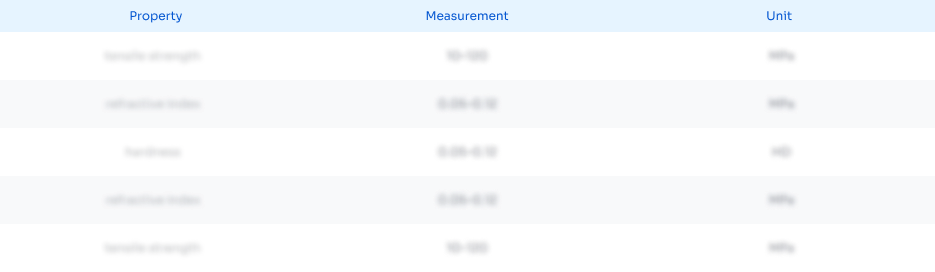
Abstract
Description
Claims
Application Information

- R&D
- Intellectual Property
- Life Sciences
- Materials
- Tech Scout
- Unparalleled Data Quality
- Higher Quality Content
- 60% Fewer Hallucinations
Browse by: Latest US Patents, China's latest patents, Technical Efficacy Thesaurus, Application Domain, Technology Topic, Popular Technical Reports.
© 2025 PatSnap. All rights reserved.Legal|Privacy policy|Modern Slavery Act Transparency Statement|Sitemap|About US| Contact US: help@patsnap.com