Mechanical part circular bead structure shape optimization method
A technology of mechanical parts and optimization methods, applied in special data processing applications, instruments, electrical digital data processing, etc., can solve problems such as poor practicability
- Summary
- Abstract
- Description
- Claims
- Application Information
AI Technical Summary
Problems solved by technology
Method used
Image
Examples
Embodiment 1
[0064] Embodiment 1: Optimizing the shape of the shoulder fillet structure in Document 1. The shaft is a structure of revolution, so only the meridian plane of the shaft can be considered. In order to simplify the calculation, the model is analyzed using the axisymmetric analysis method. In this embodiment, double-arc curves are used to optimize the shape of the shoulder fillet structure. Unless otherwise specified, the unit of length in this embodiment is mm, and the unit of angle is rad. For the sake of brevity, the text will not mark them one by one.
[0065] (a) According to the overall structural size of the shaft, in order to facilitate the use of the axisymmetric analysis method, the symmetric axis of the shaft must be consistent with the y-axis of the global Cartesian coordinate system, and the global Cartesian coordinate system x is established accordingly 0 Oy 0 , select the starting point P of the double arc 1 0 and endpoint P 2 0 , P 1 0 and P 2 0 In the ...
Embodiment 2
[0102] Embodiment 2: Optimizing the shape of the rounded corner structure of the flat plate with rounded corners in Document 2. Due to the symmetry of the flat plate structure with rounded corners, in order to simplify the calculation, a quarter of the structure is taken for analysis, and the shape optimization design of the rounded corner structure is carried out using double arc curves. Unless otherwise specified, the unit of length in this embodiment is mm, and the unit of angle is rad. For the sake of brevity, the text will not mark them one by one.
[0103] (a) According to the overall structure size of the flat plate with rounded corners, take a quarter model of the lower left corner of the structure for analysis, and establish a global Cartesian coordinate system x 0 Oy 0 , select the starting point P of the double arc 1 0 and endpoint P 2 0 , P 1 0 and P 2 0 In the global Cartesian coordinate system x 0 Oy 0 The coordinates in ( ...
PUM
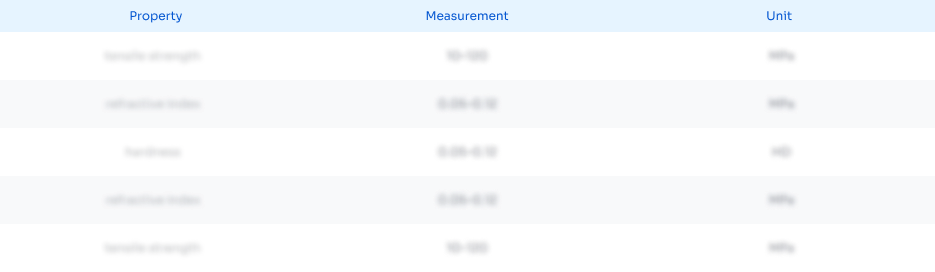
Abstract
Description
Claims
Application Information

- R&D
- Intellectual Property
- Life Sciences
- Materials
- Tech Scout
- Unparalleled Data Quality
- Higher Quality Content
- 60% Fewer Hallucinations
Browse by: Latest US Patents, China's latest patents, Technical Efficacy Thesaurus, Application Domain, Technology Topic, Popular Technical Reports.
© 2025 PatSnap. All rights reserved.Legal|Privacy policy|Modern Slavery Act Transparency Statement|Sitemap|About US| Contact US: help@patsnap.com