Method for recycling retired car polyolefin plastic parts and components by virtue of chemical foaming
A chemical foaming and polyolefin technology, which is applied in the field of chemical foaming and recycling of retired automobile polyolefin plastic parts, can solve the problem of high production cost, save materials, avoid waste of resources and environmental pollution, and achieve a simple and reliable process. Effect
- Summary
- Abstract
- Description
- Claims
- Application Information
AI Technical Summary
Problems solved by technology
Method used
Image
Examples
Embodiment 1
[0030] Example 1: Recycling method of chemical foaming of decommissioned automobile polyolefin plastic parts
[0031] The method comprises the steps of:
[0032] (1) The decommissioned automobile polypropylene bumper obtained by dismantling is cleaned and broken;
[0033] (2) The bumper reclaimed material obtained by cleaning and crushing is placed in a high-speed mixer, and blended with 0.1 parts by weight of 1250 mesh calcium carbonate, 0.1 parts by weight of titanate coupling agent 131, and antioxidant 1010 for 5 minutes;
[0034] (3) Extrude and granulate the blended bumper recycled material mixture through a twin-screw extruder according to the following process: the first zone is 160°C, the second zone is 170°C, the third zone is 200°C, and the fourth zone is 190°C ℃, five zone 180 ℃, head temperature 180 ℃, screw speed 30r / min;
[0035] (4) Put AC foaming agent and low-density polyethylene (LDPE) in a high-speed mixer at a mass ratio of 1:4 and blend for 5 minutes;
...
Embodiment 2
[0039] Example 2: Recycling method of chemical foaming of decommissioned automobile polyolefin plastic parts
[0040] The method comprises the steps of:
[0041] (1) Clean and break the PP bumper of the decommissioned automobile obtained by dismantling;
[0042] (2) The bumper recycled material obtained by cleaning and crushing is placed in a high-speed mixer, and blended with 2500 mesh calcium carbonate of 8 parts by weight, silane coupling agent KH550 of 2 parts by weight, and antioxidant 168 for 15 minutes;
[0043] (3) Extrude the blended recycled material mixture through a twin-screw extruder to obtain recycled material masterbatch according to the following process: 180°C in the first zone, 190°C in the second zone, 220°C in the third zone, 210°C in the fourth zone, The fifth zone is 200°C, the head temperature is 200°C, and the screw speed is 100r / min;
[0044] (4) Put AC foaming agent and LDPE in a high-speed mixer at a mass ratio of 1:6 and blend for 15 minutes;
...
Embodiment 3
[0048] Example 3: Recycling method of chemical foaming of decommissioned automobile polyolefin plastic parts
[0049] The method comprises the steps of:
[0050] (1) Clean and break the PP bumper of the decommissioned automobile obtained by dismantling;
[0051] (2) The bumper recycled material obtained by cleaning and crushing is placed in a high-speed mixer, and blended with 15 parts by weight of 2500 mesh calcium carbonate, 5 parts by weight of PP-g-MAH, and antioxidant B215 for 30 minutes;
[0052] (3) Extrude and granulate the blended recycled material mixture through a twin-screw extruder to obtain the recycled material masterbatch: 190°C in the first zone, 200°C in the second zone, 230°C in the third zone, 220°C in the fourth zone, The fifth zone is 210°C, the head temperature is 210°C, and the screw speed is 200r / min;
[0053] (4) Place the AC foaming agent and LDPE in a high-speed mixer at a mass ratio of 1:10 for 30 minutes;
[0054] (5) Extrude and granulate the ...
PUM
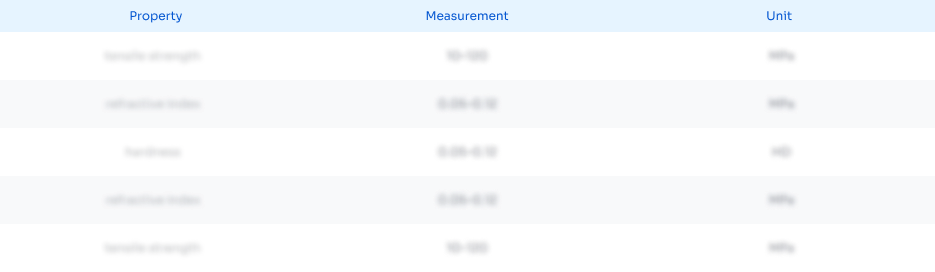
Abstract
Description
Claims
Application Information

- R&D
- Intellectual Property
- Life Sciences
- Materials
- Tech Scout
- Unparalleled Data Quality
- Higher Quality Content
- 60% Fewer Hallucinations
Browse by: Latest US Patents, China's latest patents, Technical Efficacy Thesaurus, Application Domain, Technology Topic, Popular Technical Reports.
© 2025 PatSnap. All rights reserved.Legal|Privacy policy|Modern Slavery Act Transparency Statement|Sitemap|About US| Contact US: help@patsnap.com