Method for low-temperature synthesis of polycarboxylate water reducer by using isoamyl alcohol polyether
A technology of prenol polyether and polycarboxylic acid, which is applied in the field of prenol polyether low-temperature synthesis of polycarboxylate water reducers, can solve the problems of solvent recovery, high cost, and high toxicity, and achieve simple process , cost reduction, and simple operation
- Summary
- Abstract
- Description
- Claims
- Application Information
AI Technical Summary
Problems solved by technology
Method used
Examples
Embodiment 1
[0022] In a stirring four-neck flask, put 300 parts of prenol polyether and 300 parts of water into it, raise the temperature to 10°C, until it completely melts to form a prenol polyether solution, add 5 parts of H 2 o 2 (50%) and 82 parts of H2O 2 o 2 Aqueous solution, after stirring for 10 minutes, add dropwise the acrylic acid aqueous solution of 27 parts of acrylic acid and 30 parts of water and the mixed solution of 0.1 part of L-ascorbic acid, 6 parts of thioglycolic acid and 71 parts of water, respectively. For 2.5 hours and 3 hours, after the dropwise addition, keep warm for 3 hours to carry out the copolymerization reaction. After the reaction is completed, add 28 parts of 30% sodium hydroxide aqueous solution, adjust the system pH=6.2, stir for 10min, and discharge to obtain polycarboxylic acid reduced Aqua, wherein, 5 parts H 2 o 2 (50%) and 82 parts of H2O 2 o 2 The aqueous solution is used as a reducing agent, and the added 0.1 part of L-ascorbic acid consti...
Embodiment 2
[0024] In a stirring four-neck flask, put 300 parts of prenol polyether and 200 parts of water, raise the temperature to 25 ° C, until it completely melts to form a prenol polyether solution, add 8 parts of H 2 o 2 (50%) and 82 parts of H2O 2 o 2 Aqueous solution, after stirring for 10 minutes, add dropwise the acrylic acid aqueous solution of 40 parts of acrylic acid and 5 parts of water, the mixed solution of 1 part of L-ascorbic acid, 0.2 parts of mercaptopropionic acid and 194 parts of water, the time of adding the aqueous acrylic acid solution and the mixed solution 5 hours and 5.5 hours respectively. After the dropwise addition, keep warm for 2 hours to carry out the copolymerization reaction. After the reaction is completed, add 42 parts of 30% sodium hydroxide aqueous solution to adjust the pH of the system to 7.2, stir for 10 minutes, and discharge to obtain polycarboxylic acid Water reducing agent.
Embodiment 3
[0026] In a stirring four-neck flask, put 300 parts of prenol polyether and 1200 parts of water, raise the temperature to 25 ° C, until it completely melts to form a prenol polyether solution, add 8 parts of H 2 o 2 (50%) and 82 parts of H2O 2 o 2 Aqueous solution, after stirring for 10 minutes, add dropwise the acrylic acid aqueous solution of 54 parts of acrylic acid and 18 parts of water, the mixed solution of 1 part of L-ascorbic acid, 0.2 parts of mercaptopropionic acid and 144 parts of water, and the adding time of the acrylic acid aqueous solution and the mixed solution 6 hours and 7 hours respectively. After the dropwise addition, keep warm for 1 hour to carry out the copolymerization reaction. After the reaction is completed, add 56 parts of 30% sodium hydroxide aqueous solution to adjust the pH of the system to 6.8, stir for 10 minutes, and discharge to obtain polycarboxylic acid Water reducing agent.
PUM
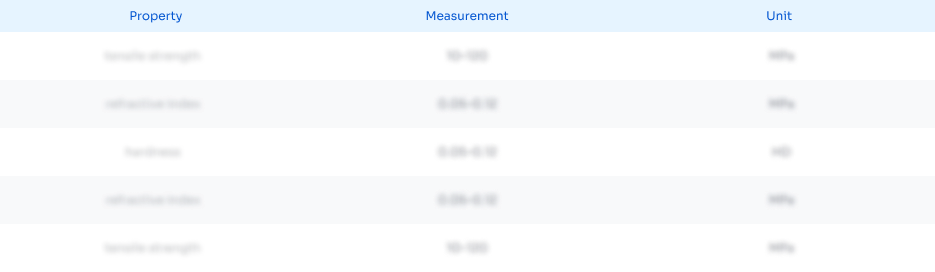
Abstract
Description
Claims
Application Information

- Generate Ideas
- Intellectual Property
- Life Sciences
- Materials
- Tech Scout
- Unparalleled Data Quality
- Higher Quality Content
- 60% Fewer Hallucinations
Browse by: Latest US Patents, China's latest patents, Technical Efficacy Thesaurus, Application Domain, Technology Topic, Popular Technical Reports.
© 2025 PatSnap. All rights reserved.Legal|Privacy policy|Modern Slavery Act Transparency Statement|Sitemap|About US| Contact US: help@patsnap.com