Parallel machine tool space dynamic accuracy detection method
A technology of dynamic accuracy and detection method, applied in measurement/indication equipment, metal processing mechanical parts, metal processing equipment, etc., can solve the problems of inability to detect some spatial positions and large differences in detection results, so as to achieve real and reliable detection data. Ease of operation, improved quality and efficiency
- Summary
- Abstract
- Description
- Claims
- Application Information
AI Technical Summary
Problems solved by technology
Method used
Image
Examples
Embodiment Construction
[0014] attached figure 1 It is a three-dimensional schematic diagram of the detection point setting of the parallel machine tool space dynamic precision detection method of the present invention, with figure 2 It is a three-dimensional schematic diagram of the adapter block of the five-coordinate dynamic precision detection tool of the present invention, with image 3 It is a schematic diagram of detecting the detection points by the space dynamic precision detection method of the parallel machine tool in the present invention, and the attached Figure 4 It is a schematic diagram of eliminating the detection blind area by using the mapping method in the present invention. In the figure, 1 is the turning block body, 2 and 3 are support arms, 4, 5 and 6 are dial gauge through holes, 7 is connecting through holes, 11 is a five-coordinate dynamic precision testing tool, 12 is a fixed rod, 13 For magnetic base, 14 is a ball nose cutter. As can be seen from the figure, the space...
PUM
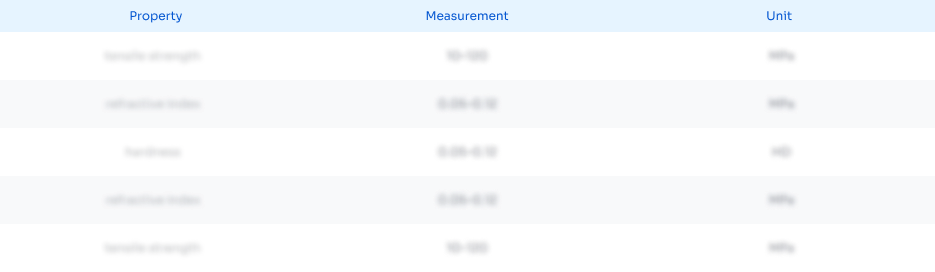
Abstract
Description
Claims
Application Information

- Generate Ideas
- Intellectual Property
- Life Sciences
- Materials
- Tech Scout
- Unparalleled Data Quality
- Higher Quality Content
- 60% Fewer Hallucinations
Browse by: Latest US Patents, China's latest patents, Technical Efficacy Thesaurus, Application Domain, Technology Topic, Popular Technical Reports.
© 2025 PatSnap. All rights reserved.Legal|Privacy policy|Modern Slavery Act Transparency Statement|Sitemap|About US| Contact US: help@patsnap.com