Ball valve flange combined rolled ring forming method
A technology of composite rolling and flange, applied in the direction of metal rolling, etc., can solve the problems of material consumption during cutting, asynchronous, and the surface groove cannot be formed completely.
- Summary
- Abstract
- Description
- Claims
- Application Information
AI Technical Summary
Problems solved by technology
Method used
Image
Examples
Embodiment ( 1
[0185] by figure 1 The ball valve flange shown is a specific example, and the upper step radius R of the rolled forging is required u , Groove radius R g , down step radius R l and the inner radius r are 728mm, 625mm, 768mm and 380mm respectively, and the height of the step on the forging is B u , groove height B g and lower step height B l They are 128mm, 176mm, and 128mm respectively. Its compound rolling ring forming method includes the following contents:
[0186] 1. Determine the shape and size of the ring blank
[0187] 1) Determine the cross-sectional shape of the ring blank. Calculate the asymmetry K of the forging according to the size of the forging s =0.3>0.15, so step ring blanks are used.
[0188] 2) Calculate the volume of the ring blank. According to the volume of the forging, the volume of the ring blank is determined as V 0 =470310947mm 3 , the ratio of the volume of the upper half of the forging to the overall forging K u =0.474, take the correct...
Embodiment ( 2
[0202] by figure 1 The ball valve flange shown is a specific example, and the upper step radius R of the rolled forging is required u , Groove radius R g , down step radius R l and the inner radius r are 90mm, 75mm, 95mm and 65mm respectively, and the height of the step on the forging is B u , groove height B g and lower step height B l They are 14mm, 26mm and 14mm respectively. Its compound rolling ring forming method includes the following contents:
[0203] 1. Determine the shape and size of the ring blank
[0204] 1) Determine the cross-sectional shape of the ring blank. Calculate the asymmetry K of the forging according to the size of the forging s =0.272>0.15, so the step ring blank is used.
[0205] 2) Calculate the volume of the ring blank. According to the volume of the forging, the volume of the ring blank is determined as V 0 =821791mm 3 , the ratio of the volume of the upper half of the forging to the overall forging K u =0.475, take the correction coe...
PUM
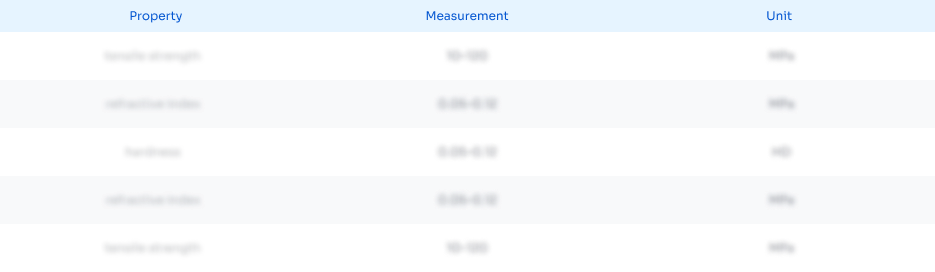
Abstract
Description
Claims
Application Information

- R&D
- Intellectual Property
- Life Sciences
- Materials
- Tech Scout
- Unparalleled Data Quality
- Higher Quality Content
- 60% Fewer Hallucinations
Browse by: Latest US Patents, China's latest patents, Technical Efficacy Thesaurus, Application Domain, Technology Topic, Popular Technical Reports.
© 2025 PatSnap. All rights reserved.Legal|Privacy policy|Modern Slavery Act Transparency Statement|Sitemap|About US| Contact US: help@patsnap.com